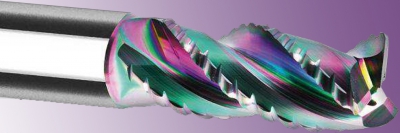
Inovatools provides a stable powerful package in the form of the high-end-HPC aluminum roughing endmill called “Primus”. Thanks to its unique design features, such as the special entwined tooth system and the optimized microgeometry, it has what it takes to rise into the ranks of the “best in the class” when it comes to aluminum roughing, according to the company.
Since Inovatools has all relevant quality factors such as design, carbide manufacture, edge preparation and coating under its own control, not only does a new tool have a short path to the user, as well as to the latest market requirements, but compliance with product quality is also guaranteed. One example of this high vertical integration is the new “Primus” series.
During a customer test in cutting aluminum 3.2315 (AlMgSi1/AlSiMgMn), the “Primus” emerges as the victor compared to a HPC-Alu-roughing end mill from the market environment, with up to 30 percent more cutting capacity. With the cutting data D1 = 20mm, ae/ap = 1xD, vc = 750 m/min, fz = 0.3 mm, “Primus” achieved a cutting volume of 4,297 cm3/min compared with the 3,008 cm3/min of the comparative tool.
“The “Primus” with inner cooling and multiturning has been systematically designed for extremely high feed rates with quiet, low-vibration running and low power consumption,” says Douglas Kline, managing director at Inovatools USA LLC. “To this end, the customer has a special entwined profile with optimized chip control as well as the high-performance coating Ta-C. For this reason, it eliminates the usual problems in cutting aluminum such as the strong adhesion tendency with built-up edges, welding deposits, caking of the chips as well as burr formation, etc.”
The VHM HPC endmill is made from well-balanced ultrafine-grained carbide, the mixture of which has been optimized to meet the special demands to which the tool is exposed.
Ta-C, combined with the cutting edge preparation in conjunction with the microgeometry, make the tool resilient. This prevents micro-chipping and makes the cutting edges more resilient. This “defect-free cutting edge design” considerably increases the service life of the “Primus”. This is supported by the entwined profile’s special chip separators. They break the aluminum chips quickly and at an early stage, and, thanks to large chip grooves, these can be rapidly transported away from the intervention zone with KSS. Not only does this bring a high level of process security, it also ensures low-vibration running for high surface quality, even during HPC roughing.
The three-edged “Primus” is available in diameter ranges from 6.00 mm to 20.00 mm, with inner cooling, multiturning and HB shank design.
Douglas Kline: “The HPC-Alu-roughing endmill ‘Primus’ is one example of how it is possible to develop latent potential, and hence an even better performance, by optimizing the design such as the microgeometry, chip control and grinding. In this way, “Primus” tools operate with minimal vibrations even at exceptionally high feed rates; for example, during the machining of aluminum for airplanes. The ‘Primus’ is already the best in class for our business partners who have tested the new tool under individual operating conditions.”
Contact Details
Related Glossary Terms
- Brinell hardness number ( HB)
Brinell hardness number ( HB)
Number related to the applied load (usually, 500 kgf and 3,000 kgf) and to the surface area of the permanent impression made by a 10mm ball indenter. The Brinell hardness number is a calculated value of the applied load (kgf) divided by the surface area of the indentation (mm2). Therefore, the unit of measure of a Brinell hardness number is kgf/mm2, but it is always omitted.
- burr
burr
Stringy portions of material formed on workpiece edges during machining. Often sharp. Can be removed with hand files, abrasive wheels or belts, wire wheels, abrasive-fiber brushes, waterjet equipment or other methods.
- edge preparation
edge preparation
Conditioning of the cutting edge, such as a honing or chamfering, to make it stronger and less susceptible to chipping. A chamfer is a bevel on the tool’s cutting edge; the angle is measured from the cutting face downward and generally varies from 25° to 45°. Honing is the process of rounding or blunting the cutting edge with abrasives, either manually or mechanically.
- endmill
endmill
Milling cutter held by its shank that cuts on its periphery and, if so configured, on its free end. Takes a variety of shapes (single- and double-end, roughing, ballnose and cup-end) and sizes (stub, medium, long and extra-long). Also comes with differing numbers of flutes.
- feed
feed
Rate of change of position of the tool as a whole, relative to the workpiece while cutting.
- grinding
grinding
Machining operation in which material is removed from the workpiece by a powered abrasive wheel, stone, belt, paste, sheet, compound, slurry, etc. Takes various forms: surface grinding (creates flat and/or squared surfaces); cylindrical grinding (for external cylindrical and tapered shapes, fillets, undercuts, etc.); centerless grinding; chamfering; thread and form grinding; tool and cutter grinding; offhand grinding; lapping and polishing (grinding with extremely fine grits to create ultrasmooth surfaces); honing; and disc grinding.
- milling machine ( mill)
milling machine ( mill)
Runs endmills and arbor-mounted milling cutters. Features include a head with a spindle that drives the cutters; a column, knee and table that provide motion in the three Cartesian axes; and a base that supports the components and houses the cutting-fluid pump and reservoir. The work is mounted on the table and fed into the rotating cutter or endmill to accomplish the milling steps; vertical milling machines also feed endmills into the work by means of a spindle-mounted quill. Models range from small manual machines to big bed-type and duplex mills. All take one of three basic forms: vertical, horizontal or convertible horizontal/vertical. Vertical machines may be knee-type (the table is mounted on a knee that can be elevated) or bed-type (the table is securely supported and only moves horizontally). In general, horizontal machines are bigger and more powerful, while vertical machines are lighter but more versatile and easier to set up and operate.
- shank
shank
Main body of a tool; the portion of a drill or similar end-held tool that fits into a collet, chuck or similar mounting device.