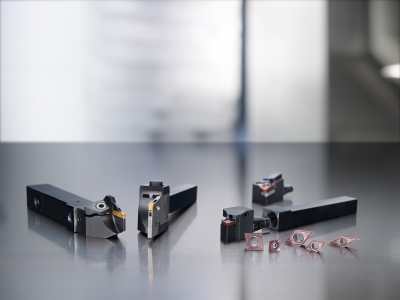
Seco Tools has introduced a modular toolholder system for manufacturers seeking to improve their productivity with Swiss-style machining. The system enables fast, easy and repeatable insert indexing and tool changes outside of tight machine work spaces. The QC (quick-change) Toolholders also feature Seco Jetstream Tooling and Jetstream Tooling Duo technology for optimal chip control, high-quality surface finishes and extended tool life.
For ease of use, the Seco QC Modular Toolholder allows users to remove both cutting heads and inserts as a single assembly, quickly index them and reinstall. Manufacturers may also use this system to exchange cutting heads and inserts with a second set for even greater efficiency. The QC cutting head also features double carbide pins for accurate, consistent and secure insert mounting and indexing.
Seco Jetstream Tooling technology precisely directs high-pressure coolant through the QC Toolholder to the cutting zone. Seco Jetstream Tooling Duo, available on a selection of cutting heads, adds a second coolant channel to the underside of the holder. The second coolant channel can be switched off if needed for even more versatile machining.
The new QC Toolholders include cutting heads for general ISO turning, MDT, threading and parting-off. Shanks are available in metric sizes of 10 mm, 12 mm and 16 mm, and inch sizes of 0.375", 0.500" and 0.625".
Contact Details
Related Glossary Terms
- coolant
coolant
Fluid that reduces temperature buildup at the tool/workpiece interface during machining. Normally takes the form of a liquid such as soluble or chemical mixtures (semisynthetic, synthetic) but can be pressurized air or other gas. Because of water’s ability to absorb great quantities of heat, it is widely used as a coolant and vehicle for various cutting compounds, with the water-to-compound ratio varying with the machining task. See cutting fluid; semisynthetic cutting fluid; soluble-oil cutting fluid; synthetic cutting fluid.
- threading
threading
Process of both external (e.g., thread milling) and internal (e.g., tapping, thread milling) cutting, turning and rolling of threads into particular material. Standardized specifications are available to determine the desired results of the threading process. Numerous thread-series designations are written for specific applications. Threading often is performed on a lathe. Specifications such as thread height are critical in determining the strength of the threads. The material used is taken into consideration in determining the expected results of any particular application for that threaded piece. In external threading, a calculated depth is required as well as a particular angle to the cut. To perform internal threading, the exact diameter to bore the hole is critical before threading. The threads are distinguished from one another by the amount of tolerance and/or allowance that is specified. See turning.
- toolholder
toolholder
Secures a cutting tool during a machining operation. Basic types include block, cartridge, chuck, collet, fixed, modular, quick-change and rotating.
- turning
turning
Workpiece is held in a chuck, mounted on a face plate or secured between centers and rotated while a cutting tool, normally a single-point tool, is fed into it along its periphery or across its end or face. Takes the form of straight turning (cutting along the periphery of the workpiece); taper turning (creating a taper); step turning (turning different-size diameters on the same work); chamfering (beveling an edge or shoulder); facing (cutting on an end); turning threads (usually external but can be internal); roughing (high-volume metal removal); and finishing (final light cuts). Performed on lathes, turning centers, chucking machines, automatic screw machines and similar machines.