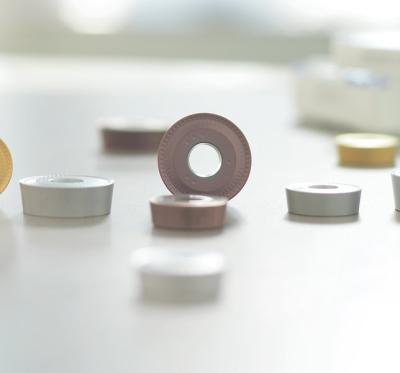
Shops that struggle to manage metalworking chips and optimize tool life in extreme turning applications will benefit from the new Seco -R3 and -RR93 insert geometries. As part of the RCMX and RCMT range of turning inserts, the new geometries make easy work of such challenging applications as turning railway car wheels.
The new inserts combine roughing and medium finishing chipbreakers with Duratomic grade technology. The -RR93 chipbreaker boosts tool life, improves productivity, increases product reliability, enhances chip management and impart a fine surface finish. This new design replaces the -RR94 geometry.
For medium finishing applications in steels, difficult stainless steels and superalloys, the -R3 geometry offers optimally positioned grooves that control chips even at depths of cut as small as 0.059" (1.5 mm), at high feed rates from 0.024 ipr to 0.047 ipr (0.6 mm/rev to 1.2 mm/rev) and at cutting speeds from 3.543 ipm to 6.299 ipm (90 m/min. to 160 m/min). (Within these cutting-data ranges, the correct choices depend on the application at hand.) The -R3 geometry replaces the previous -R2 geometry.
To produce smoother finishes ideal for the surface areas of railway wheels, as well as for medium roughing applications with difficult-to-cut materials, RCMT20-R3 positive screw-clamped additions to the range reduce machining vibration significantly. Dedicated insert edge treatments and retained functional toughness arrest comb cracks and increase edge security.
The new RCMX and RCMT geometries feature the Duratomic CVD aluminum-oxide coating process that optimizes mechanical and thermal properties for enhanced performance. This technology also provides used edge detection to reduce insert cutting-edge waste.
The new -RR93 and -R3 geometries and Duratomic grades have been tested in most common railway wheel materials, including R7, R8, R9, M1, Class B and Class C.
Contact Details
Related Glossary Terms
- chemical vapor deposition ( CVD)
chemical vapor deposition ( CVD)
High-temperature (1,000° C or higher), atmosphere-controlled process in which a chemical reaction is induced for the purpose of depositing a coating 2µm to 12µm thick on a tool’s surface. See coated tools; PVD, physical vapor deposition.
- chipbreaker
chipbreaker
Groove or other tool geometry that breaks chips into small fragments as they come off the workpiece. Designed to prevent chips from becoming so long that they are difficult to control, catch in turning parts and cause safety problems.
- feed
feed
Rate of change of position of the tool as a whole, relative to the workpiece while cutting.
- inches per minute ( ipm)
inches per minute ( ipm)
Value that refers to how far the workpiece or cutter advances linearly in 1 minute, defined as: ipm = ipt 5 number of effective teeth 5 rpm. Also known as the table feed or machine feed.
- metalworking
metalworking
Any manufacturing process in which metal is processed or machined such that the workpiece is given a new shape. Broadly defined, the term includes processes such as design and layout, heat-treating, material handling and inspection.
- stainless steels
stainless steels
Stainless steels possess high strength, heat resistance, excellent workability and erosion resistance. Four general classes have been developed to cover a range of mechanical and physical properties for particular applications. The four classes are: the austenitic types of the chromium-nickel-manganese 200 series and the chromium-nickel 300 series; the martensitic types of the chromium, hardenable 400 series; the chromium, nonhardenable 400-series ferritic types; and the precipitation-hardening type of chromium-nickel alloys with additional elements that are hardenable by solution treating and aging.
- superalloys
superalloys
Tough, difficult-to-machine alloys; includes Hastelloy, Inconel and Monel. Many are nickel-base metals.
- turning
turning
Workpiece is held in a chuck, mounted on a face plate or secured between centers and rotated while a cutting tool, normally a single-point tool, is fed into it along its periphery or across its end or face. Takes the form of straight turning (cutting along the periphery of the workpiece); taper turning (creating a taper); step turning (turning different-size diameters on the same work); chamfering (beveling an edge or shoulder); facing (cutting on an end); turning threads (usually external but can be internal); roughing (high-volume metal removal); and finishing (final light cuts). Performed on lathes, turning centers, chucking machines, automatic screw machines and similar machines.