Contact Details
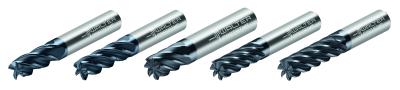
With the introduction of more than 3,000 new cutting tools in inch sizes, Walter takes the lead in solid carbide milling. This expansion includes shoulder/slot mills for cutting super alloys and other high-temperature alloys, titanium and stainless steel (ISO S and M material groups) at the highest level.
The MA377/MA373 Supreme milling cutters (4,5 and 6 flutes) for machining titanium and stainless steels are available in sizes from 1/8 to 1¼ inch diameter. The tools are available with or without corner radii, and with or without chip splitters. With Walter’s optimized tool coatings, these mills are suitable for slotting, peripheral milling, trochoidal milling and high-efficiency milling. The offered chipbreaker reduces chip nesting issues and deflection stemming from excess tool pressure.
The MD177/MD173 Supreme milling cutters (7 flutes) have more teeth to boost productivity when machining titanium and high-temperature alloys. The tools are available in sizes from ¼ to 1 inch diameter. The uneven pitch on the tools reduces vibration and allows the entire length of the cutting edge to be used to provide uniform wear. The cutting tools supply outstanding productivity and process reliability.
The MD177 cutter creates exceptionally smooth surfaces without “waterlines.” The MD173 is equipped with chipbreakers that provide outstanding process reliability with high metal removal rates.
The MA375 Supreme cutter (4,5 and 7 flutes) is for roughing and finishing Inconel and other nickel-base super alloys. The tool is available in sizes from 1/8 to 1 inch diameter and features a variable helix and variable indexing to help reduce chatter and boost productivity. The 4 and 5 flute versions are for aggressive slotting up to ½ inch diameter, peripheral milling and trochoidal machining. The 7-flute mill is designed for dynamic machining and excels at high workpiece hardness levels.
The Walter lineup of products consists of three categories of tools. Supreme tools indicate the highest level of technology and performance available. Advance tools indicate products efficiently balanced between price and performance and Perform tools are products that provide an economical solution with focused importance on price.
Related Glossary Terms
- alloys
alloys
Substances having metallic properties and being composed of two or more chemical elements of which at least one is a metal.
- chatter
chatter
Condition of vibration involving the machine, workpiece and cutting tool. Once this condition arises, it is often self-sustaining until the problem is corrected. Chatter can be identified when lines or grooves appear at regular intervals in the workpiece. These lines or grooves are caused by the teeth of the cutter as they vibrate in and out of the workpiece and their spacing depends on the frequency of vibration.
- chipbreaker
chipbreaker
Groove or other tool geometry that breaks chips into small fragments as they come off the workpiece. Designed to prevent chips from becoming so long that they are difficult to control, catch in turning parts and cause safety problems.
- gang cutting ( milling)
gang cutting ( milling)
Machining with several cutters mounted on a single arbor, generally for simultaneous cutting.
- hardness
hardness
Hardness is a measure of the resistance of a material to surface indentation or abrasion. There is no absolute scale for hardness. In order to express hardness quantitatively, each type of test has its own scale, which defines hardness. Indentation hardness obtained through static methods is measured by Brinell, Rockwell, Vickers and Knoop tests. Hardness without indentation is measured by a dynamic method, known as the Scleroscope test.
- milling
milling
Machining operation in which metal or other material is removed by applying power to a rotating cutter. In vertical milling, the cutting tool is mounted vertically on the spindle. In horizontal milling, the cutting tool is mounted horizontally, either directly on the spindle or on an arbor. Horizontal milling is further broken down into conventional milling, where the cutter rotates opposite the direction of feed, or “up” into the workpiece; and climb milling, where the cutter rotates in the direction of feed, or “down” into the workpiece. Milling operations include plane or surface milling, endmilling, facemilling, angle milling, form milling and profiling.
- milling machine ( mill)
milling machine ( mill)
Runs endmills and arbor-mounted milling cutters. Features include a head with a spindle that drives the cutters; a column, knee and table that provide motion in the three Cartesian axes; and a base that supports the components and houses the cutting-fluid pump and reservoir. The work is mounted on the table and fed into the rotating cutter or endmill to accomplish the milling steps; vertical milling machines also feed endmills into the work by means of a spindle-mounted quill. Models range from small manual machines to big bed-type and duplex mills. All take one of three basic forms: vertical, horizontal or convertible horizontal/vertical. Vertical machines may be knee-type (the table is mounted on a knee that can be elevated) or bed-type (the table is securely supported and only moves horizontally). In general, horizontal machines are bigger and more powerful, while vertical machines are lighter but more versatile and easier to set up and operate.
- peripheral milling
peripheral milling
Form of milling that produces a finished surface generally in a plane parallel to the rotating axis of a cutter having teeth or inserts on the periphery of the cutter body. See milling.
- pitch
pitch
1. On a saw blade, the number of teeth per inch. 2. In threading, the number of threads per inch.
- slotting
slotting
Machining, normally milling, that creates slots, grooves and similar recesses in workpieces, including T-slots and dovetails.
- stainless steels
stainless steels
Stainless steels possess high strength, heat resistance, excellent workability and erosion resistance. Four general classes have been developed to cover a range of mechanical and physical properties for particular applications. The four classes are: the austenitic types of the chromium-nickel-manganese 200 series and the chromium-nickel 300 series; the martensitic types of the chromium, hardenable 400 series; the chromium, nonhardenable 400-series ferritic types; and the precipitation-hardening type of chromium-nickel alloys with additional elements that are hardenable by solution treating and aging.