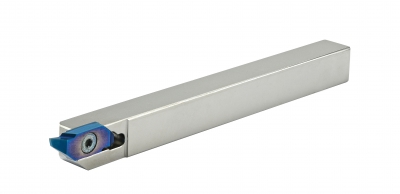
Carmex Precision Tools LLC has announced the latest addition to its family of tooling for Swiss-style applications. The Swiss-Line combines a new type of polygon insert and holder for external turning, grooving, parting and threading. The precision ground inserts are constructed of solid carbide with specialty coating for longer tool life and increased productivity, according to the company.
Developed for machining a wide range of materials, a selection of inserts can be used with the same toolholders. Holders are coated to resist abrasion for a long service life.
According to Jim White, national sales manager for Carmex USA, “Our new polygon inserts have been specially designed and constructed to deliver high-precision performance, excellent finish and greater production in Swiss-style machining applications. The polygon shape, combined with Carmex’s special clamping system, allows for fast changeover, and the carbide/coating combination is engineered to withstand the stresses of hard machining in a small-parts environment. The Swiss-Line polygon inserts and toolholders are another example of our continuing commitment to the increasing number of customers using Swiss-style machining.”
Contact Details
Related Glossary Terms
- grooving
grooving
Machining grooves and shallow channels. Example: grooving ball-bearing raceways. Typically performed by tools that are capable of light cuts at high feed rates. Imparts high-quality finish.
- parting
parting
When used in lathe or screw-machine operations, this process separates a completed part from chuck-held or collet-fed stock by means of a very narrow, flat-end cutting, or parting, tool.
- threading
threading
Process of both external (e.g., thread milling) and internal (e.g., tapping, thread milling) cutting, turning and rolling of threads into particular material. Standardized specifications are available to determine the desired results of the threading process. Numerous thread-series designations are written for specific applications. Threading often is performed on a lathe. Specifications such as thread height are critical in determining the strength of the threads. The material used is taken into consideration in determining the expected results of any particular application for that threaded piece. In external threading, a calculated depth is required as well as a particular angle to the cut. To perform internal threading, the exact diameter to bore the hole is critical before threading. The threads are distinguished from one another by the amount of tolerance and/or allowance that is specified. See turning.
- turning
turning
Workpiece is held in a chuck, mounted on a face plate or secured between centers and rotated while a cutting tool, normally a single-point tool, is fed into it along its periphery or across its end or face. Takes the form of straight turning (cutting along the periphery of the workpiece); taper turning (creating a taper); step turning (turning different-size diameters on the same work); chamfering (beveling an edge or shoulder); facing (cutting on an end); turning threads (usually external but can be internal); roughing (high-volume metal removal); and finishing (final light cuts). Performed on lathes, turning centers, chucking machines, automatic screw machines and similar machines.