Contact Details
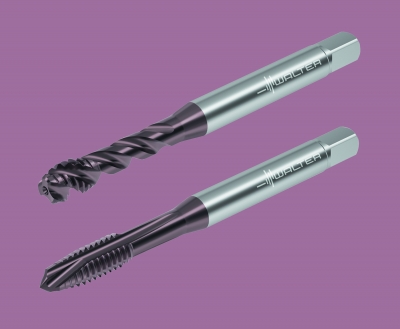
Walter has announced the introduction of the TC117/TC217 Advance cut taps for high threading productivity in a wide range of different materials. The Advance lineup is one of the three categories to Walter threading tools. The Advance line signifies product that is efficiently balanced between price and performance. The others are Perform tools that provide an economical solution with focused importance on price and the Supreme line indicating the highest level of technology and performance available.
The versatile TC117 (blind-hole) and TC217 (through-hole) taps tackle material ranging from steel to aluminum (ISO material groups P, M, K and N), materials up to 370 HB and because of this versatility can help save on inventory costs by reducing the number of taps needed. The TC117 blind-hole tap has a 40° helix angle and up to 2.5 x DN with chamfer form C (semi bottoming) or E (full bottoming). The TC217 through-hole tap features a spiral point for forward chip evacuation and a thread depth capability of 3.0 × DN. Both taps use HSS-E substrate that provides enhanced durability due to its cobalt enrichment.
The new sizes include UNC thread styles, giving these flexible taps an even wider range of application in a variety of materials. The taps feature WY80RG for good chip control, good wear resistance and higher cutting speeds and WY80FC, which sacrifices wear resistance and cutting speeds but offers much better chip control for stringy and difficult-to-control chips such as stainless steel. Dimension range includes UNC 1-64 to UNC 2 1/2-6; UNF 0-80 to UNF 1 1/4-12; UN 1 1/8-8 to UN 1 5/8-8; UNS 1-14; STIUNC 2-56 to STIUNC 3/8-16; STIUNF 10-32 to STIUNF 3/8-24; and M3 to M20, all offered with DIN length/ANSI shank (DIN/ANSI standard).
Related Glossary Terms
- Brinell hardness number ( HB)
Brinell hardness number ( HB)
Number related to the applied load (usually, 500 kgf and 3,000 kgf) and to the surface area of the permanent impression made by a 10mm ball indenter. The Brinell hardness number is a calculated value of the applied load (kgf) divided by the surface area of the indentation (mm2). Therefore, the unit of measure of a Brinell hardness number is kgf/mm2, but it is always omitted.
- blind-hole
blind-hole
Hole or cavity cut in a solid shape that does not connect with other holes or exit through the workpiece.
- helix angle
helix angle
Angle that the tool’s leading edge makes with the plane of its centerline.
- shank
shank
Main body of a tool; the portion of a drill or similar end-held tool that fits into a collet, chuck or similar mounting device.
- tap
tap
Cylindrical tool that cuts internal threads and has flutes to remove chips and carry tapping fluid to the point of cut. Normally used on a drill press or tapping machine but also may be operated manually. See tapping.
- threading
threading
Process of both external (e.g., thread milling) and internal (e.g., tapping, thread milling) cutting, turning and rolling of threads into particular material. Standardized specifications are available to determine the desired results of the threading process. Numerous thread-series designations are written for specific applications. Threading often is performed on a lathe. Specifications such as thread height are critical in determining the strength of the threads. The material used is taken into consideration in determining the expected results of any particular application for that threaded piece. In external threading, a calculated depth is required as well as a particular angle to the cut. To perform internal threading, the exact diameter to bore the hole is critical before threading. The threads are distinguished from one another by the amount of tolerance and/or allowance that is specified. See turning.
- through-hole
through-hole
Hole or cavity cut in a solid shape that connects with other holes or extends all the way through the workpiece.
- wear resistance
wear resistance
Ability of the tool to withstand stresses that cause it to wear during cutting; an attribute linked to alloy composition, base material, thermal conditions, type of tooling and operation and other variables.