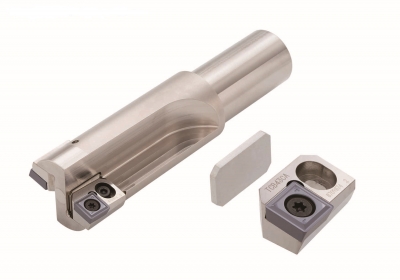
Tungaloy’s counterboring tools, TCB series, is now available with new tool diameters, ranging from 26 mm to 59 mm or 1.02” to 2.32”, and inserts with the –CG style chipbreaker geometry.
The TCB series was initially developed to countersink JIS-designated cap screws, thus offering limited tool diameters in the standard range. In today’s diverse boring market, however, manufacturers are resorting to diameter-specific tailor-made boring tools or end mills to enlarge existing hole diameters, compromising productivity and lead times. Driven by these market needs, Tungaloy has introduced an additional tool diameter range to its TCB series, ranging from 26.0 mm to 59.0 mm or 1.02” to 2.32” along with the new –CG style chipbreaker, which yields excellent chip flow in various materials at a range of cutting depths.
The expanded TCB line incorporates a cartridge design for easy diameter adjustments. The diameter can be adjusted by placing multiple-sized shims between the tool body and cartridge, enabling a single tool body to machine various diameters. Fine diameter adjustments in increments of 0.1 mm or .004” are also possible with thinner shims sold separately.
The enhanced TCB series now offers a high efficient standard tooling solution, which is readily available for not only boring and hole enlargement applications, but also I.D. turning and boring on lathe machines.
At a glance:
Enhanced tool diameters, ranging from 26 mm to 59 mm or 1.02” to 2.32” now offers various counterboring solutions with standard tools – eliminates the hassle for ordering tailor-built tools and waiting long lead times.
Cartridge design allows a single tool to machine multiple diameters.
Enables high efficient machining.
Improved productivity and cost-efficiency thanks to the latest AH6030 grade and new –CG style chipbreaker for excellent chip flow in any type of materials at various cutting depths.
Contact Details
Related Glossary Terms
- boring
boring
Enlarging a hole that already has been drilled or cored. Generally, it is an operation of truing the previously drilled hole with a single-point, lathe-type tool. Boring is essentially internal turning, in that usually a single-point cutting tool forms the internal shape. Some tools are available with two cutting edges to balance cutting forces.
- chipbreaker
chipbreaker
Groove or other tool geometry that breaks chips into small fragments as they come off the workpiece. Designed to prevent chips from becoming so long that they are difficult to control, catch in turning parts and cause safety problems.
- counterboring
counterboring
Enlarging one end of a drilled hole. The enlarged hole, which is concentric with the original hole, is flat on the bottom. Counterboring is used primarily to set bolt heads and nuts below the workpiece surface.
- countersink
countersink
Tool that cuts a sloped depression at the top of a hole to permit a screw head or other object to rest flush with the surface of the workpiece.
- lathe
lathe
Turning machine capable of sawing, milling, grinding, gear-cutting, drilling, reaming, boring, threading, facing, chamfering, grooving, knurling, spinning, parting, necking, taper-cutting, and cam- and eccentric-cutting, as well as step- and straight-turning. Comes in a variety of forms, ranging from manual to semiautomatic to fully automatic, with major types being engine lathes, turning and contouring lathes, turret lathes and numerical-control lathes. The engine lathe consists of a headstock and spindle, tailstock, bed, carriage (complete with apron) and cross slides. Features include gear- (speed) and feed-selector levers, toolpost, compound rest, lead screw and reversing lead screw, threading dial and rapid-traverse lever. Special lathe types include through-the-spindle, camshaft and crankshaft, brake drum and rotor, spinning and gun-barrel machines. Toolroom and bench lathes are used for precision work; the former for tool-and-die work and similar tasks, the latter for small workpieces (instruments, watches), normally without a power feed. Models are typically designated according to their “swing,” or the largest-diameter workpiece that can be rotated; bed length, or the distance between centers; and horsepower generated. See turning machine.
- turning
turning
Workpiece is held in a chuck, mounted on a face plate or secured between centers and rotated while a cutting tool, normally a single-point tool, is fed into it along its periphery or across its end or face. Takes the form of straight turning (cutting along the periphery of the workpiece); taper turning (creating a taper); step turning (turning different-size diameters on the same work); chamfering (beveling an edge or shoulder); facing (cutting on an end); turning threads (usually external but can be internal); roughing (high-volume metal removal); and finishing (final light cuts). Performed on lathes, turning centers, chucking machines, automatic screw machines and similar machines.