Contact Details
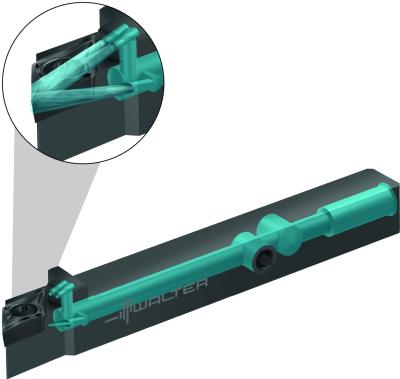
With its new Walter Turn Swiss toolholders for turning applications, Walter is targeting applications on Swiss-style automatic lathes and multi-spindle machines that have up to 2,175 psi (150 bar) of coolant pressure. The holders are suitable for turning high-precision parts, longitudinal (axial) turning, facing and copy turning small-diameter components.
The holder provides targeted clearance face cooling for efficient chip control and increased tool life in addition to high precision cooling on the flank face to slow down the insert heat and wear. The holders feature a flexible coolant connection in three positions for either external plumbing or thru-coolant introduction through late turrets.
The holders accept CCGT3xx, DCGT3xx and VCGT2xx indexable inserts and provide a high level of indexing accuracy even when turning parts with tight tolerance specifications. The short head dimension enables short clamping and high stability. The shank dimensions are 12 mm × 12 mm and 16 mm × 16 mm.
Potential benefits include less downtime caused by bird nesting of chips thanks to the targeted clearance face cooling and long tool life even when turning heat-resistant workpiece materials due to the cooled cutting edge.
Compared to the exchangeable head systems available in the market, the Walter Turn Swiss holder will provide significantly higher stability due to mono-block solid design. This in turn leads to significantly higher tool life with less vibrations, as well as higher surface finish quality of the finished workpieces.
In addition to the conventional ISO turning toolholders, the W1011-S-P copy turning/profiling systems with positive engagement and the G4014-P grooving tools with side clamping are also part of the precision cooling ‘-P’ style Walter Turn Swiss holder program offering.
Related Glossary Terms
- clearance
clearance
Space provided behind a tool’s land or relief to prevent rubbing and subsequent premature deterioration of the tool. See land; relief.
- coolant
coolant
Fluid that reduces temperature buildup at the tool/workpiece interface during machining. Normally takes the form of a liquid such as soluble or chemical mixtures (semisynthetic, synthetic) but can be pressurized air or other gas. Because of water’s ability to absorb great quantities of heat, it is widely used as a coolant and vehicle for various cutting compounds, with the water-to-compound ratio varying with the machining task. See cutting fluid; semisynthetic cutting fluid; soluble-oil cutting fluid; synthetic cutting fluid.
- grooving
grooving
Machining grooves and shallow channels. Example: grooving ball-bearing raceways. Typically performed by tools that are capable of light cuts at high feed rates. Imparts high-quality finish.
- shank
shank
Main body of a tool; the portion of a drill or similar end-held tool that fits into a collet, chuck or similar mounting device.
- tolerance
tolerance
Minimum and maximum amount a workpiece dimension is allowed to vary from a set standard and still be acceptable.
- turning
turning
Workpiece is held in a chuck, mounted on a face plate or secured between centers and rotated while a cutting tool, normally a single-point tool, is fed into it along its periphery or across its end or face. Takes the form of straight turning (cutting along the periphery of the workpiece); taper turning (creating a taper); step turning (turning different-size diameters on the same work); chamfering (beveling an edge or shoulder); facing (cutting on an end); turning threads (usually external but can be internal); roughing (high-volume metal removal); and finishing (final light cuts). Performed on lathes, turning centers, chucking machines, automatic screw machines and similar machines.