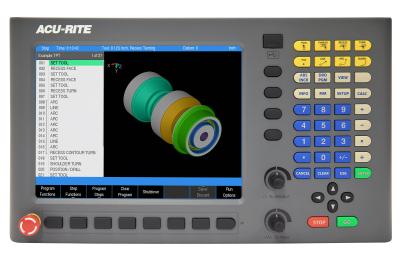
Offering lathe machinists a new easy-to-use turning control with state-of-the-art features as standard, HEIDENHAIN presents the highly anticipated ACU-RITE brand TURNPWR control. The new TURNPWR control is a workshop-oriented turning control that enables the user to program conventional machining operations right at the machine in an easy-to-use conversational programming language. It is designed for turning machine tools with up to two axes.
TURNPWR (see short video) was developed to satisfy the wants and needs of lathe machinists where manual and automated operation are both useful and needed. TURNPWR promises to enable the user to maximize throughput by significantly reducing set-up time, scrap and other non-productive operations, thereby increasing efficiency, productivity and profitability.
The well-known ACU-RITE conversational programming format for controls is a user-friendly method of writing part programs and included in the TURNPWR, however G-code (ISO) programming can also be used. Basic editing of G-code programs is also possible.
On the new TURNPWR, a 12.1” high-resolution display boasts a screen layout that is clearly arranged and user friendly. Preview graphics in the editor illustrate the individual machining steps for programming the contour as well as corresponding tool path generated using only dimensions pulled from a production drawing. It also accepts DXF files.
TURNPWR is a closed-loop system with positioning feedback provided by rotary encoders inside the motor assemblies. When fitted with the (optional) ACU-RITE precision glass scales (1 µm/0.00005” resolution), TURNPWR also includes Position-Trac™, an advanced unique feature that enables the user to easily, quickly and accurately re-establish work piece zero after shutting down or power loss.
Contact Details
Related Glossary Terms
- closed-loop system
closed-loop system
CNC system in which the program output, or the distance the slide moves, is measured and compared to the program input. The system automatically adjusts the output to be the same as the input.
- conversational programming
conversational programming
Method for using plain English to produce G-code file without knowing G-code in order to program CNC machines.
- lathe
lathe
Turning machine capable of sawing, milling, grinding, gear-cutting, drilling, reaming, boring, threading, facing, chamfering, grooving, knurling, spinning, parting, necking, taper-cutting, and cam- and eccentric-cutting, as well as step- and straight-turning. Comes in a variety of forms, ranging from manual to semiautomatic to fully automatic, with major types being engine lathes, turning and contouring lathes, turret lathes and numerical-control lathes. The engine lathe consists of a headstock and spindle, tailstock, bed, carriage (complete with apron) and cross slides. Features include gear- (speed) and feed-selector levers, toolpost, compound rest, lead screw and reversing lead screw, threading dial and rapid-traverse lever. Special lathe types include through-the-spindle, camshaft and crankshaft, brake drum and rotor, spinning and gun-barrel machines. Toolroom and bench lathes are used for precision work; the former for tool-and-die work and similar tasks, the latter for small workpieces (instruments, watches), normally without a power feed. Models are typically designated according to their “swing,” or the largest-diameter workpiece that can be rotated; bed length, or the distance between centers; and horsepower generated. See turning machine.
- turning
turning
Workpiece is held in a chuck, mounted on a face plate or secured between centers and rotated while a cutting tool, normally a single-point tool, is fed into it along its periphery or across its end or face. Takes the form of straight turning (cutting along the periphery of the workpiece); taper turning (creating a taper); step turning (turning different-size diameters on the same work); chamfering (beveling an edge or shoulder); facing (cutting on an end); turning threads (usually external but can be internal); roughing (high-volume metal removal); and finishing (final light cuts). Performed on lathes, turning centers, chucking machines, automatic screw machines and similar machines.
- turning machine
turning machine
Any machine that rotates a workpiece while feeding a cutting tool into it. See lathe.