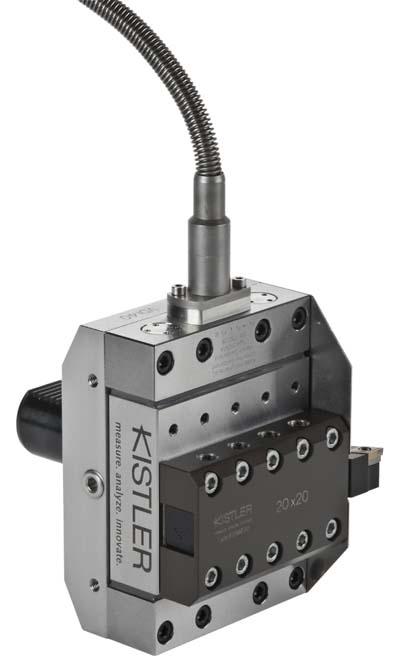
Kistler has introduced the Type 9129A, a three-component system, designed to offer high-precision measurements of cutting tool machinery forces of up to 8 kN, when turning outside and inside turret lathe diameters, in support of critical manufacturing process monitoring requirements.
The modular Kistler Type 9129A system consists of a dynamometer with corrosion-resistant construction that is further impenetrable to coolants. The dynamometer is comprised of four integral three-component force sensors, the outputs of which are passed to its corresponding 9-way flange socket. The force sensors are mounted with electrical ground isolation under high preload conditions between the cover plate and two lateral base plates, a specialized mounting technique which allows for minimal temperature errors, as well as force measurements achieved with virtually no displacement. The ground isolation of the force sensors largely prevents EMI and ground loop interference from compromising measurement integrity. When used in conjunction with Kistler Type 1687B and Type 1689B connecting cables, the dynamometer is environmentally protected to IP67 standards.
Designed for direct compatibility with industry disk-type turret cutting tool machinery, the Type 9129A is further offered with machinery adapters for VDI tool holding fixtures with 30mm, 40mm and 50mm diameters; Coromant Capto C5 and C6 clamping units; direct tool holding fixtures with 20mm x 40mm or 25mm x 50mm footprint; tool holders for external turning tools measuring 20mm x 20mm or 25mm x 25mm; and tool holders for internal turning tools with 25mm, 32mm or 40mm diameters. The unique technical features and specifications of the Kistler Type 9129A allow for simultaneous measurement of the three cutting forces while turning outside and inside diameters on lathes with turret-type tool heads. In addition, as a stand-alone, the Kistler Type 9129A dynamometer is suitable as a general purpose, multi-component force measurement device, able to be mounted without accessories directly onto a flat base plate.
Recommended for use with the Kistler Type 9129A cutting force measurement system, sold separately, is the Kistler Type 2825A DynoWare, a universal data acquisition and analysis software product. The simple operation of DynoWare allows for full configuration and control of up to 28 force measurement channels via USB, RS-232C or IEEE-488, with real-time visualization of measured curves, along with evaluation and calculation functions. The software allows for acquisition and evaluation of cutting force data, along with measured data storage.
Contact Details
Related Glossary Terms
- cutting force
cutting force
Engagement of a tool’s cutting edge with a workpiece generates a cutting force. Such a cutting force combines tangential, feed and radial forces, which can be measured by a dynamometer. Of the three cutting force components, tangential force is the greatest. Tangential force generates torque and accounts for more than 95 percent of the machining power. See dynamometer.
- dynamometer
dynamometer
When drilling, a device for measuring the generated torque and axial force (thrust). When milling, a device for measuring the generated torque and feed force. When turning, a device for measuring the tangential, feed and radial forces.
- flat ( screw flat)
flat ( screw flat)
Flat surface machined into the shank of a cutting tool for enhanced holding of the tool.
- lathe
lathe
Turning machine capable of sawing, milling, grinding, gear-cutting, drilling, reaming, boring, threading, facing, chamfering, grooving, knurling, spinning, parting, necking, taper-cutting, and cam- and eccentric-cutting, as well as step- and straight-turning. Comes in a variety of forms, ranging from manual to semiautomatic to fully automatic, with major types being engine lathes, turning and contouring lathes, turret lathes and numerical-control lathes. The engine lathe consists of a headstock and spindle, tailstock, bed, carriage (complete with apron) and cross slides. Features include gear- (speed) and feed-selector levers, toolpost, compound rest, lead screw and reversing lead screw, threading dial and rapid-traverse lever. Special lathe types include through-the-spindle, camshaft and crankshaft, brake drum and rotor, spinning and gun-barrel machines. Toolroom and bench lathes are used for precision work; the former for tool-and-die work and similar tasks, the latter for small workpieces (instruments, watches), normally without a power feed. Models are typically designated according to their “swing,” or the largest-diameter workpiece that can be rotated; bed length, or the distance between centers; and horsepower generated. See turning machine.
- turning
turning
Workpiece is held in a chuck, mounted on a face plate or secured between centers and rotated while a cutting tool, normally a single-point tool, is fed into it along its periphery or across its end or face. Takes the form of straight turning (cutting along the periphery of the workpiece); taper turning (creating a taper); step turning (turning different-size diameters on the same work); chamfering (beveling an edge or shoulder); facing (cutting on an end); turning threads (usually external but can be internal); roughing (high-volume metal removal); and finishing (final light cuts). Performed on lathes, turning centers, chucking machines, automatic screw machines and similar machines.
- turret lathe
turret lathe
Differs from engine lathe in that the normal compound rest is replaced by pivoting, multitool turrets mounted on the cross slide and tailstock. See lathe.