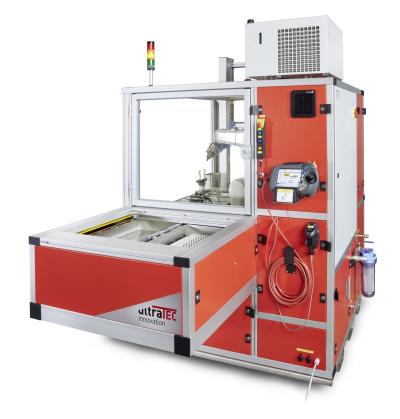
Now available from VOLLMER is the exciting new UltraTEC ultrasonic A25 deburring machine. As part of the VOLLMER Group, UltraTEC is a company that has won a number of awards for its patented new ultrasonic deburring method that only uses water. Without the use of chemicals, the UltraTEC deburring system has already been recognized as a validated process in a variety of industry sectors.
Only formed in 2019, UltraTEC has taken the industry by storm with its unique technology that utilizes an ultrasonic horn that oscillates to generate sound waves as well as cavitation to clean and deburr external and internal edges with complete process reliability. The environmentally friendly solution provides sharp edged burr-free parts that often cannot be processed via alternate methods. This energy efficient system eliminates common challenges when deburring parts such as deformation, discoloring and changes to the oxide layer on the component. It also performs on small and delicate components that cannot be processed via alternative methods. This makes the UltraTEC ultrasonic A25 perfect for applications in heavily regulated sectors with challenging demands such as the medical, food and drug industries, aerospace, electronics and many more.
How it works
The UltraTEC ultrasonic A25 creates a formation and dissolution/implosion of bubbles in water that release an intense energy during implosion. This is created by an ultra-high oscillation of 20kHz (20,000 oscillations per second) with an oscillation width of +/-80-120microns, which far exceeds the amplitude of ultrasonic cleaning, cutting and welding technologies. An ultrasonic horn that is fully submersed in water is set into resonant vibration via mechanical oscillations to transmit the extremely high forces into the water tank. With horn diameters from 1.2 to 14mm, the ultrasonic horn is fixed in a position in the water tank and components are robotically moved around the ultrasonic horn that creates a cavitation jet from 250 to 270m/s that breaks burrs from the parts.
The UltraTEC ultrasonic A25 is configured with an ultrasonic stainless steel 40 liter basin that can accommodate parts up to 150 by 150 by 150mm and weighing up to 1.5kg. In the basin are two opposing ultrasonic horns to cater for a variety of applications and once processed, parts are moved to a compressed air-drying station. Components are collected from an external pallet by a 6-axis ABB industrial robot that is programmed via an application integrated into the ABB RobotStudio suite – a CAM system for ultrasonic deburring.
The UltraTEC ultrasonic A25 is a completely flexible system with a multitude of options such as conveyor loading and different component tray configurations. Additional options include various waterproof gripping systems for part picking, a selection of motor and air pressure spindles for additional processes like brushing and re-gripping stations to turn components around for gripping from the opposite side.
Contact Details
Related Glossary Terms
- brushing
brushing
Generic term for a curve whose shape is controlled by a combination of its control points and knots (parameter values). The placement of the control points is controlled by an application-specific combination of order, tangency constraints and curvature requirements. See NURBS, nonuniform rational B-splines.
- computer-aided manufacturing ( CAM)
computer-aided manufacturing ( CAM)
Use of computers to control machining and manufacturing processes.
- industrial robot
industrial robot
Robot designed for industrial use. Primarily used as a material-handling device but also used for changing tools, assembling parts, and manipulating special tools and measuring devices. Depending on design, an industrial robot can be programmed to perform a task by means of a controller, or it can be “walked” through the required movements by utilizing a digitizing system that translates movements into commands that the robot can be “taught.” See robot; teaching pendant.
- ultrasonic cleaning
ultrasonic cleaning
Method of cleaning metal or plastic parts by immersing them in an aqueous or solvent-based cleaning solution and imposing ultrasound energy on the bath to enhance cleaning by creating cavitation conditions at the part surface, which imparts a strong scouring action to remove tenacious soils.