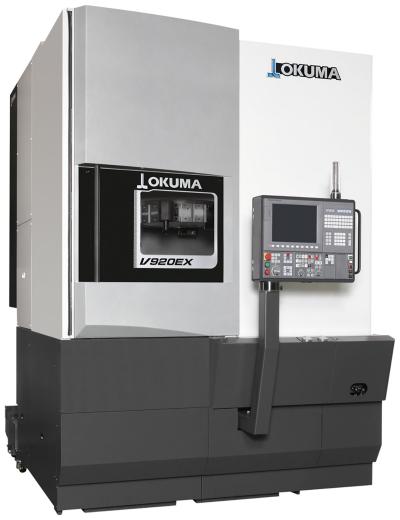
Okuma’s new V920EX one-saddle, vertical lathe features a powerful turning spindle and a large work envelope, making it ideal for cutting a variety of large, heavy parts. The V920EX boasts a work envelope with a maximum turning diameter of 36.22" and 33.86" of swing over the saddle enabling it to accommodate large, odd–shaped workpieces. Highly rigid construction and powerful ballscrews generate slideway movement to both axes for precise machining of heavy parts, according to the company.
Maximum machining productivity is achieved with a V12 turret and foolproof chip discharge. Designed for smooth chip flow, optional side or rear chip conveyors can be placed to match discharge direction based on shop floor requirements. Maintenance tasks are simplified with easy access to the air filter, hydraulic unit and coolant tank on the back of the machine.
Okuma’s Thermo-Friendly Concept is standard and automatically compensates ambient temperature changes to maintain tight tolerances. Cycle times, lead times, and energy costs are significantly improved with Okuma’s open architecture OSP-P300L control and ECO suite feature.
Key features of Okuma’s V920EX vertical lathe:
Max Turning Diameter in Ø 36.22/33.86
Max Swing in Ø 39.37
Max Cutting Length in 33.86
Turret Type V12
RPM Range 20 to 1,250
Floor Space (in) 88.646 x 112.01
Weight (lb) 25,133
Contact Details
Related Glossary Terms
- coolant
coolant
Fluid that reduces temperature buildup at the tool/workpiece interface during machining. Normally takes the form of a liquid such as soluble or chemical mixtures (semisynthetic, synthetic) but can be pressurized air or other gas. Because of water’s ability to absorb great quantities of heat, it is widely used as a coolant and vehicle for various cutting compounds, with the water-to-compound ratio varying with the machining task. See cutting fluid; semisynthetic cutting fluid; soluble-oil cutting fluid; synthetic cutting fluid.
- lathe
lathe
Turning machine capable of sawing, milling, grinding, gear-cutting, drilling, reaming, boring, threading, facing, chamfering, grooving, knurling, spinning, parting, necking, taper-cutting, and cam- and eccentric-cutting, as well as step- and straight-turning. Comes in a variety of forms, ranging from manual to semiautomatic to fully automatic, with major types being engine lathes, turning and contouring lathes, turret lathes and numerical-control lathes. The engine lathe consists of a headstock and spindle, tailstock, bed, carriage (complete with apron) and cross slides. Features include gear- (speed) and feed-selector levers, toolpost, compound rest, lead screw and reversing lead screw, threading dial and rapid-traverse lever. Special lathe types include through-the-spindle, camshaft and crankshaft, brake drum and rotor, spinning and gun-barrel machines. Toolroom and bench lathes are used for precision work; the former for tool-and-die work and similar tasks, the latter for small workpieces (instruments, watches), normally without a power feed. Models are typically designated according to their “swing,” or the largest-diameter workpiece that can be rotated; bed length, or the distance between centers; and horsepower generated. See turning machine.
- turning
turning
Workpiece is held in a chuck, mounted on a face plate or secured between centers and rotated while a cutting tool, normally a single-point tool, is fed into it along its periphery or across its end or face. Takes the form of straight turning (cutting along the periphery of the workpiece); taper turning (creating a taper); step turning (turning different-size diameters on the same work); chamfering (beveling an edge or shoulder); facing (cutting on an end); turning threads (usually external but can be internal); roughing (high-volume metal removal); and finishing (final light cuts). Performed on lathes, turning centers, chucking machines, automatic screw machines and similar machines.
- work envelope
work envelope
Cube, sphere, cylinder or other physical space within which the cutting tool is capable of reaching.