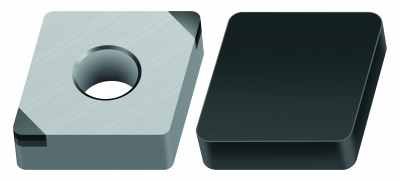
Walter has introduced WBK20 and WBK30, new CBN grades that bring higher levels of productivity and reliability to the machining of cast iron and hardened steel. Both new grades have edge-preparation designs that have been optimized for their target applications.
With its tipped configuration, WBK20 is exceptionally wear resistant and well suited for finishing of cast iron or powered metal workpieces. Because of the higher CBN content it is also well suited for roughing in hard turning applications. With its full CBN configuration and high CBN content, WBK30 is ideal for heavy depth of cuts, roughing in cast irons, powder metals and exceptionally hard and tough applications, such as interrupted cuts, in hard turning.
These new grades complement Walter's previously released WBH10C coated CBN and WBH10 and WBH20 CBN grade ideal for high temperature stability in hard metal turning. These inserts also have the option of chip breaker (TM-M2) for trouble shooting and wiper (MW2) for exceptional surface finish or higher feed and productivity. Various standard ISO turning insert shapes with these new grades, such as C, D, S and T, are available in both positive and negative clearance geometries. Select grades WBS10 and WBH20 are also available as grooving inserts for aerospace alloys and hard steels respectively.
Contact Details
Related Glossary Terms
- alloys
alloys
Substances having metallic properties and being composed of two or more chemical elements of which at least one is a metal.
- cast irons
cast irons
Cast ferrous alloys containing carbon in excess of solubility in austenite that exists in the alloy at the eutectic temperature. Cast irons include gray cast iron, white cast iron, malleable cast iron and ductile, or nodular, cast iron. The word “cast” is often left out.
- clearance
clearance
Space provided behind a tool’s land or relief to prevent rubbing and subsequent premature deterioration of the tool. See land; relief.
- cubic boron nitride ( CBN)
cubic boron nitride ( CBN)
Crystal manufactured from boron nitride under high pressure and temperature. Used to cut hard-to-machine ferrous and nickel-base materials up to 70 HRC. Second hardest material after diamond. See superabrasive tools.
- feed
feed
Rate of change of position of the tool as a whole, relative to the workpiece while cutting.
- grooving
grooving
Machining grooves and shallow channels. Example: grooving ball-bearing raceways. Typically performed by tools that are capable of light cuts at high feed rates. Imparts high-quality finish.
- hard turning
hard turning
Single-point cutting of a workpiece that has a hardness value higher than 45 HRC.
- lapping compound( powder)
lapping compound( powder)
Light, abrasive material used for finishing a surface.
- turning
turning
Workpiece is held in a chuck, mounted on a face plate or secured between centers and rotated while a cutting tool, normally a single-point tool, is fed into it along its periphery or across its end or face. Takes the form of straight turning (cutting along the periphery of the workpiece); taper turning (creating a taper); step turning (turning different-size diameters on the same work); chamfering (beveling an edge or shoulder); facing (cutting on an end); turning threads (usually external but can be internal); roughing (high-volume metal removal); and finishing (final light cuts). Performed on lathes, turning centers, chucking machines, automatic screw machines and similar machines.
- wiper
wiper
Metal-removing edge on the face of a cutter that travels in a plane perpendicular to the axis. It is the edge that sweeps the machined surface. The flat should be as wide as the feed per revolution of the cutter. This allows any given insert to wipe the entire workpiece surface and impart a fine surface finish at a high feed rate.