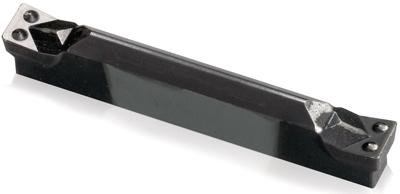
Job shops around the world may have business and customer requirements unique to each company, but concerns on how to improve costs and secure more business are common to all. "Shops want more performance options, and at the same time don't want multiple, job- or material-specific tooling solutions tying up their inventory," says Mark Filosemi, global product manager, threading, grooving, and cut-off for WIDIA. "Where productivity is concerned, particularly in grooving, and cut-off, you have to have a versatile system to be serious. That's where the WIDIA WMT platform is a proven winner, because shops can do more with it."
Now that platform is expanding with the addition of the new high-performance PH geometry, designed and engineered for plunging and turning in materials harder than 35 HRC or in heavily interrupted cuts across a broad range of work materials.
The new PH geometry fits in with the proven features that make WIDIA's WMT platform a core program for grooving, and cut-off. One toolholder securely seats whatever insert geometries are needed: PT for plunging and turning, PC for plunging and contouring, CM for cut-off (or CM-W with wiper), and the new PH geometry for plunging and turning hard materials.
The WMT toolholder is engineered with an extra-long clamping area for excellent insert stability. The proprietary "Double V" system makes it easy to securely seat inserts in the toolholder pocket for both optimal insert positioning and superior side-load resistance. Such precise insert positioning and overall system rigidity both translate into notably improved accuracy and tool life, whether it's face grooving, ID grooving, OD grooving, plunging, or profiling that needs to be done.
With its 90-degree top and bottom clamping design, rigid cutting edges, and positive geometry, the new PH WMT insert is the first choice for plunging and turning hard materials or in accomplishing interrupted cuts in steels, stainless steels, aluminums, cast irons, or high-temperature alloys. The recommended WU25PT grade for interrupted cutting features an advanced PVD TiAlN coating for longer tool life, equating to more parts per edge.
"Whether companies are familiar with the WMT system or coming to it for the first time, the value remains: one toolholder, multiple options," Filosemi says. "Adding the new PH geometry for plunging and turning hard materials or doing interrupted cuts gives shops more options to get the jobs done."
Contact Details
Related Glossary Terms
- alloys
alloys
Substances having metallic properties and being composed of two or more chemical elements of which at least one is a metal.
- cast irons
cast irons
Cast ferrous alloys containing carbon in excess of solubility in austenite that exists in the alloy at the eutectic temperature. Cast irons include gray cast iron, white cast iron, malleable cast iron and ductile, or nodular, cast iron. The word “cast” is often left out.
- grooving
grooving
Machining grooves and shallow channels. Example: grooving ball-bearing raceways. Typically performed by tools that are capable of light cuts at high feed rates. Imparts high-quality finish.
- inner diameter ( ID)
inner diameter ( ID)
Dimension that defines the inside diameter of a cavity or hole. See OD, outer diameter.
- outer diameter ( OD)
outer diameter ( OD)
Dimension that defines the exterior diameter of a cylindrical or round part. See ID, inner diameter.
- physical vapor deposition ( PVD)
physical vapor deposition ( PVD)
Tool-coating process performed at low temperature (500° C), compared to chemical vapor deposition (1,000° C). Employs electric field to generate necessary heat for depositing coating on a tool’s surface. See CVD, chemical vapor deposition.
- profiling
profiling
Machining vertical edges of workpieces having irregular contours; normally performed with an endmill in a vertical spindle on a milling machine or with a profiler, following a pattern. See mill, milling machine.
- stainless steels
stainless steels
Stainless steels possess high strength, heat resistance, excellent workability and erosion resistance. Four general classes have been developed to cover a range of mechanical and physical properties for particular applications. The four classes are: the austenitic types of the chromium-nickel-manganese 200 series and the chromium-nickel 300 series; the martensitic types of the chromium, hardenable 400 series; the chromium, nonhardenable 400-series ferritic types; and the precipitation-hardening type of chromium-nickel alloys with additional elements that are hardenable by solution treating and aging.
- threading
threading
Process of both external (e.g., thread milling) and internal (e.g., tapping, thread milling) cutting, turning and rolling of threads into particular material. Standardized specifications are available to determine the desired results of the threading process. Numerous thread-series designations are written for specific applications. Threading often is performed on a lathe. Specifications such as thread height are critical in determining the strength of the threads. The material used is taken into consideration in determining the expected results of any particular application for that threaded piece. In external threading, a calculated depth is required as well as a particular angle to the cut. To perform internal threading, the exact diameter to bore the hole is critical before threading. The threads are distinguished from one another by the amount of tolerance and/or allowance that is specified. See turning.
- titanium aluminum nitride ( TiAlN)
titanium aluminum nitride ( TiAlN)
Often used as a tool coating. AlTiN indicates the aluminum content is greater than the titanium. See coated tools.
- toolholder
toolholder
Secures a cutting tool during a machining operation. Basic types include block, cartridge, chuck, collet, fixed, modular, quick-change and rotating.
- turning
turning
Workpiece is held in a chuck, mounted on a face plate or secured between centers and rotated while a cutting tool, normally a single-point tool, is fed into it along its periphery or across its end or face. Takes the form of straight turning (cutting along the periphery of the workpiece); taper turning (creating a taper); step turning (turning different-size diameters on the same work); chamfering (beveling an edge or shoulder); facing (cutting on an end); turning threads (usually external but can be internal); roughing (high-volume metal removal); and finishing (final light cuts). Performed on lathes, turning centers, chucking machines, automatic screw machines and similar machines.