Contact Details
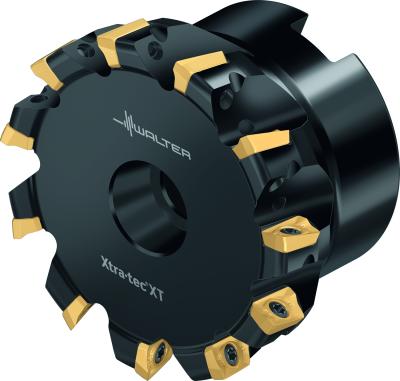
Walter has expanded the popular offering for one of its newest milling families, the Xtra·tec® XT M5130 shoulder milling cutter. Many of the design features focus on making the tool body more productive by increasing the strength. In addition, it also features a new mounting position for the inserts and 17% more teeth.
These enhancements to the Xtra·tec XT M5130 milling cutter, including a new clearance angle of 7° have added to this universal tool's existing benefits of high performance, high surface quality, exceptional reliability and safety, and outstanding versatility. The M5130 handles a wide array of machining operations including face, shoulder, ramping and pocket milling, as well as circular interpolation operations. This versatile mill is well suited to machining steel, stainless steel, cast iron, non-ferrous material and materials with difficult cutting properties.
This wide range of applications results in lower tooling and administrative costs, as does the fact that its 90° approach angle dramatically decreases the need for finishing operations.
The Xtra·tec® XT M5130 Shoulder Milling Cutter features two pitches for different applications, and a stable cross section due to the modified installation position of the indexable inserts. Available in diameters of 0.5-6.0 in. (10-160 mm), and geometries: F55, an exceptionally stable geometry; G55, a universal grade for medium machining conditions; K55, a light cutting geometry; and M85, for aluminum machining, low cutting forces, and sharp cutting edges.
Related Glossary Terms
- approach angle
approach angle
Angle between the insert’s side-cutting edge and the line perpendicular to the milling cutter’s axis of rotation. Approach angle, which is also known as cutting edge angle, is used with metric units of measurement. See lead angle.
- clearance
clearance
Space provided behind a tool’s land or relief to prevent rubbing and subsequent premature deterioration of the tool. See land; relief.
- gang cutting ( milling)
gang cutting ( milling)
Machining with several cutters mounted on a single arbor, generally for simultaneous cutting.
- interpolation
interpolation
Process of generating a sufficient number of positioning commands for the servomotors driving the machine tool so the path of the tool closely approximates the ideal path. See CNC, computer numerical control; NC, numerical control.
- milling
milling
Machining operation in which metal or other material is removed by applying power to a rotating cutter. In vertical milling, the cutting tool is mounted vertically on the spindle. In horizontal milling, the cutting tool is mounted horizontally, either directly on the spindle or on an arbor. Horizontal milling is further broken down into conventional milling, where the cutter rotates opposite the direction of feed, or “up” into the workpiece; and climb milling, where the cutter rotates in the direction of feed, or “down” into the workpiece. Milling operations include plane or surface milling, endmilling, facemilling, angle milling, form milling and profiling.
- milling cutter
milling cutter
Loosely, any milling tool. Horizontal cutters take the form of plain milling cutters, plain spiral-tooth cutters, helical cutters, side-milling cutters, staggered-tooth side-milling cutters, facemilling cutters, angular cutters, double-angle cutters, convex and concave form-milling cutters, straddle-sprocket cutters, spur-gear cutters, corner-rounding cutters and slitting saws. Vertical cutters use shank-mounted cutting tools, including endmills, T-slot cutters, Woodruff keyseat cutters and dovetail cutters; these may also be used on horizontal mills. See milling.
- milling machine ( mill)
milling machine ( mill)
Runs endmills and arbor-mounted milling cutters. Features include a head with a spindle that drives the cutters; a column, knee and table that provide motion in the three Cartesian axes; and a base that supports the components and houses the cutting-fluid pump and reservoir. The work is mounted on the table and fed into the rotating cutter or endmill to accomplish the milling steps; vertical milling machines also feed endmills into the work by means of a spindle-mounted quill. Models range from small manual machines to big bed-type and duplex mills. All take one of three basic forms: vertical, horizontal or convertible horizontal/vertical. Vertical machines may be knee-type (the table is mounted on a knee that can be elevated) or bed-type (the table is securely supported and only moves horizontally). In general, horizontal machines are bigger and more powerful, while vertical machines are lighter but more versatile and easier to set up and operate.