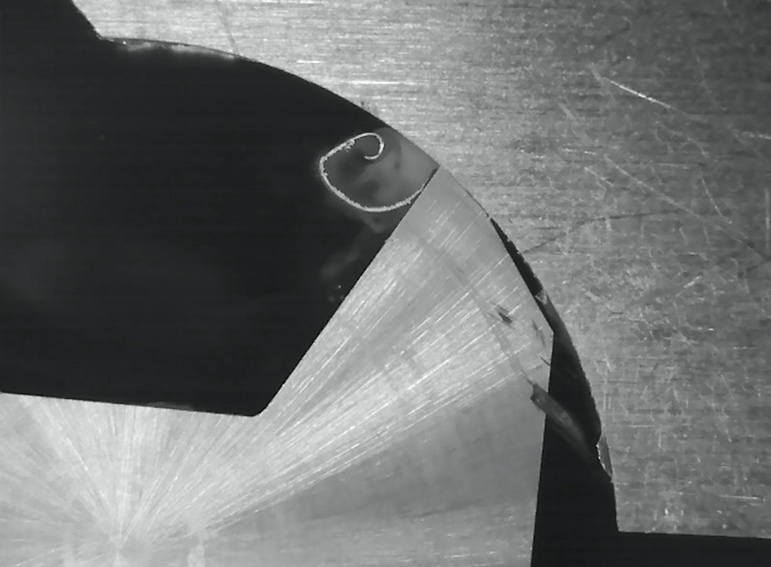
The research and development team at Blaser Swisslube, a Swiss expert in metalworking fluids, set about planning and implementing an idea to capture a machining process, chip formation and the behavior of the metalworking fluid more precisely than ever before through photos and videos. The idea came about as part of a joint project with the renowned ETH Zurich.
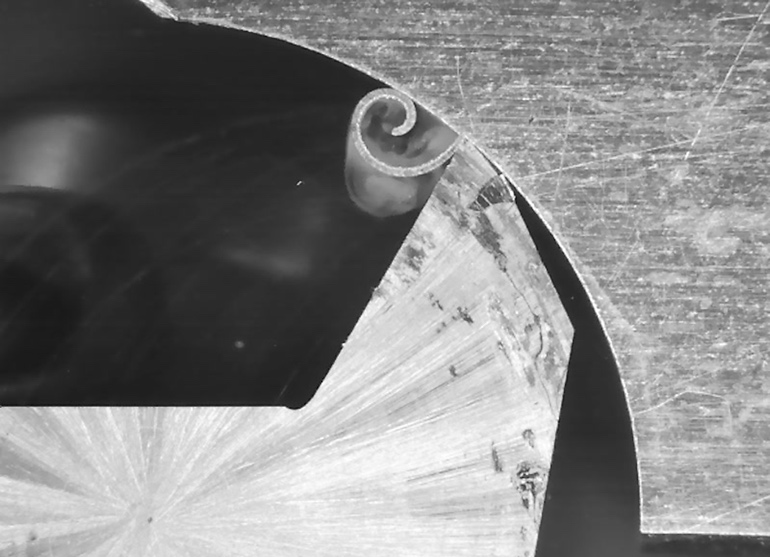
The use of a high-speed camera with a macro lens, which is placed behind a sight glass to keep the metalworking fluid at a distance, should make uniquely sharp, precise recordings possible. A ring light was used to provide the necessary light intensity, as well as a carbide cutter with a helix angle of 0° that was specially ground for this particular test.
The researchers say that the results are fascinating. The high-speed recordings showed for the first time that the mechanism of action of oil-free, water-soluble metalworking fluid, Synergy 735 – namely its improved lubricating effect at higher temperatures – also occurs during machining and is fast enough to optimize milling processes. Synergy 735 thus changes its properties and adapts to the machining process like a chameleon.
“Our Technology Center allows us to take a closer look than our competitors. This focus on all the details and the cooperation between our chemists and the machining experts enables us to develop metalworking fluids that improve processes sustainably, reduce production costs and prolong tool life,” said Marc Blaser, CEO of Blaser Swisslube.
As the Synergy 735 metalworking fluid used in the test described cools down, it becomes clear again, keeping the machine clean and allowing a good view of the machining process. The advantages also include the neutral odor and excellent skin compatibility. Synergy 735 provides flawless finishes on a variety of materials from aluminum and titanium alloys to CrNi steels. The minimal foaming means the coolant is also ideally suited to high-pressure systems.
Blaser Swisslube’s Technology Center has been undergoing continuous expansion for more than 10 years. At present, research is carried out using four CNC milling machines and a state-of-the-art grinding machine in a facility covering an area of more than 1,500 m² (16‘146 sq ft). New developments are tested and customers’ production situations are simulated under realistic conditions. High-precision measuring devices and sensors enable the data acquired to be interpreted correctly.
Measuring wear reveals potential savings
For example, a microscope camera for measuring wear automatically takes microscopic images of the turning plate every two minutes. “Tool wear often limits the economic viability of a process. The new measuring options give us meaningful information, directly from the machine,” explains Dr. Linus Meier, a tribology specialist at Blaser Swisslube.
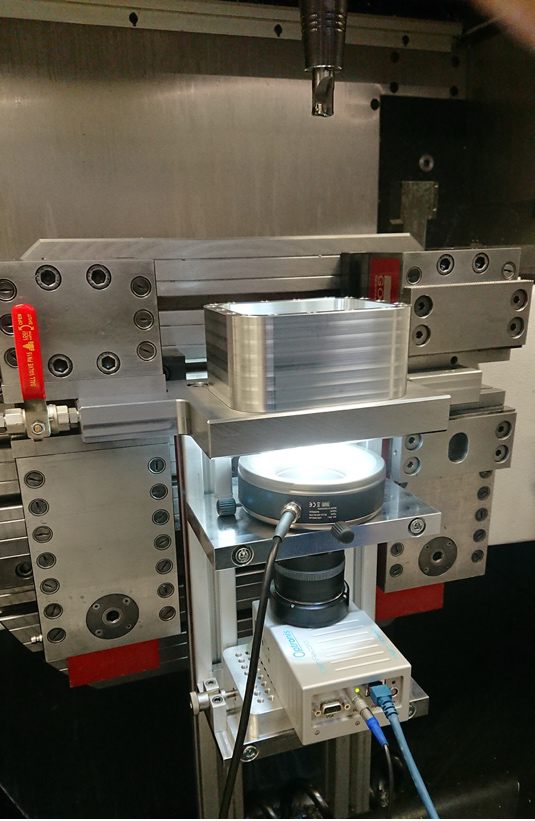
The optimized data flow means that changes to the metalworking fluid can be implemented more quickly and easily. “This is good news for our customers. That’s because high-performance metalworking fluids offer enormous savings potential in production, whether through increased productivity or reduced tool wear,” emphasizes Linus Meier.
A holistic look
The perfect metalworking fluid often requires more than a dozen ingredients, including oils, emulsifiers and additives: producing a metalworking fluid to serve as a liquid tool that optimizes the efficiency of the entire production process, requires both sophisticated formulations from our researchers and manufacturing expertise from our machining technologists.
Blaser Swisslube has relied on the collaboration between both disciplines for some time now. Marc Blaser: “Only if our specialist chemists are able to get to know the coolant on site as part of a performance test and then interpret the data acquired by the manufacturing technologists, are we able to make great progress in metalworking fluid development.”
Contact Details
Related Glossary Terms
- alloys
alloys
Substances having metallic properties and being composed of two or more chemical elements of which at least one is a metal.
- computer numerical control ( CNC)
computer numerical control ( CNC)
Microprocessor-based controller dedicated to a machine tool that permits the creation or modification of parts. Programmed numerical control activates the machine’s servos and spindle drives and controls the various machining operations. See DNC, direct numerical control; NC, numerical control.
- coolant
coolant
Fluid that reduces temperature buildup at the tool/workpiece interface during machining. Normally takes the form of a liquid such as soluble or chemical mixtures (semisynthetic, synthetic) but can be pressurized air or other gas. Because of water’s ability to absorb great quantities of heat, it is widely used as a coolant and vehicle for various cutting compounds, with the water-to-compound ratio varying with the machining task. See cutting fluid; semisynthetic cutting fluid; soluble-oil cutting fluid; synthetic cutting fluid.
- gang cutting ( milling)
gang cutting ( milling)
Machining with several cutters mounted on a single arbor, generally for simultaneous cutting.
- grinding
grinding
Machining operation in which material is removed from the workpiece by a powered abrasive wheel, stone, belt, paste, sheet, compound, slurry, etc. Takes various forms: surface grinding (creates flat and/or squared surfaces); cylindrical grinding (for external cylindrical and tapered shapes, fillets, undercuts, etc.); centerless grinding; chamfering; thread and form grinding; tool and cutter grinding; offhand grinding; lapping and polishing (grinding with extremely fine grits to create ultrasmooth surfaces); honing; and disc grinding.
- grinding machine
grinding machine
Powers a grinding wheel or other abrasive tool for the purpose of removing metal and finishing workpieces to close tolerances. Provides smooth, square, parallel and accurate workpiece surfaces. When ultrasmooth surfaces and finishes on the order of microns are required, lapping and honing machines (precision grinders that run abrasives with extremely fine, uniform grits) are used. In its “finishing” role, the grinder is perhaps the most widely used machine tool. Various styles are available: bench and pedestal grinders for sharpening lathe bits and drills; surface grinders for producing square, parallel, smooth and accurate parts; cylindrical and centerless grinders; center-hole grinders; form grinders; facemill and endmill grinders; gear-cutting grinders; jig grinders; abrasive belt (backstand, swing-frame, belt-roll) grinders; tool and cutter grinders for sharpening and resharpening cutting tools; carbide grinders; hand-held die grinders; and abrasive cutoff saws.
- helix angle
helix angle
Angle that the tool’s leading edge makes with the plane of its centerline.
- metalworking
metalworking
Any manufacturing process in which metal is processed or machined such that the workpiece is given a new shape. Broadly defined, the term includes processes such as design and layout, heat-treating, material handling and inspection.
- milling
milling
Machining operation in which metal or other material is removed by applying power to a rotating cutter. In vertical milling, the cutting tool is mounted vertically on the spindle. In horizontal milling, the cutting tool is mounted horizontally, either directly on the spindle or on an arbor. Horizontal milling is further broken down into conventional milling, where the cutter rotates opposite the direction of feed, or “up” into the workpiece; and climb milling, where the cutter rotates in the direction of feed, or “down” into the workpiece. Milling operations include plane or surface milling, endmilling, facemilling, angle milling, form milling and profiling.
- turning
turning
Workpiece is held in a chuck, mounted on a face plate or secured between centers and rotated while a cutting tool, normally a single-point tool, is fed into it along its periphery or across its end or face. Takes the form of straight turning (cutting along the periphery of the workpiece); taper turning (creating a taper); step turning (turning different-size diameters on the same work); chamfering (beveling an edge or shoulder); facing (cutting on an end); turning threads (usually external but can be internal); roughing (high-volume metal removal); and finishing (final light cuts). Performed on lathes, turning centers, chucking machines, automatic screw machines and similar machines.