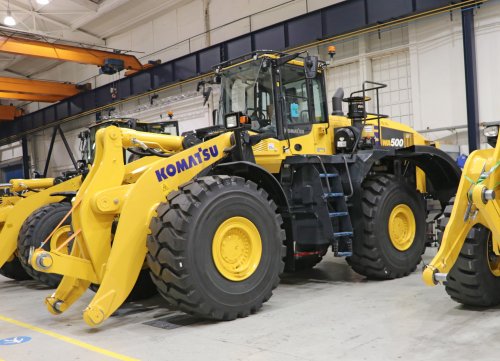
An Ecomill traveling column milling machine by Emco Mecof has been used in Komatsu Germany‘s production since March 2021. Acquired as a replacement for two older machining centers, the Ecomill has since been saving space and working hours and increased the Hanover-based construction machinery manufacturer‘s productivity.
Modern construction vehicles perfectly customized to meet a wide variety of requirements are crucial to the industry. The Japanese Komatsu Group has been established in this market for decades.
The same applies to Komatsu Germany GmbH, a Hanover-based company that had been known under the name of “Hanomag AG” until 2002. Focusing on the development and manufacturing of wheel bearings and mobile excavators for the whole of Europe, the German subsidiary has been growing for years. According to managing director Ingo Buescher, the Corona-related crisis had certainly made its presence felt, albeit to a moderate extent.
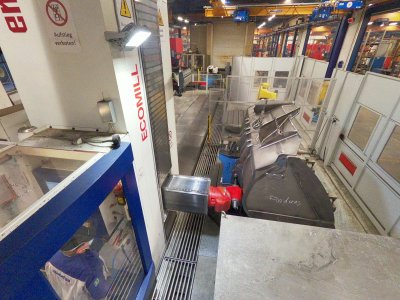
“This year has been marked by a substantial growth of roughly 70 percent, which more than compensates for the previously experienced decline,” said Buescher.
Several aspects have influenced this positive development. One of the key factors: Komatsu Germany produces premium vehicles which meet the highest standards. “The market is aware of that,” said Buescher.
Another crucial factor, he said is that the Hanover-based company is no longer focusing on classic earth-moving machinery only, but has rather been expanding its lines of business to include further industrial applications, such as waste management, steel production, and port handling.
“It‘s not as if we were reinventing the wheel for each of our customers,” he said. “Our exworks solutions are always based on a tried and tested basic machine. Here at Hanover, we cooperate with our customers to develop options for them that will maximize productivity for applications that can sometimes be quite exotic. Thanks to highly digitized processes, we mostly use standard production procedures.”
But, the Hanover-based company‘s capabilities go beyond that. “Our customers cannot wait indefinitely for their wheel bearings and mobile excavators to be delivered. They need them as soon as possible. Our internal processes allow us to manufacture and deliver a customized construction machine within four weeks after receiving the order,” he said.
According to Buescher, two crucial factors have paved the way for that ability” highly qualified employees and company-wide digitization and modern technologies and machines are characterized by maximum reliability, flexibility and quality.
Ecomill replaced two machining centers
In March 2021, Komatsu Germany integrated an Ecomill traveling column milling machine by Emco Mecof into its mechanical production. Designed for pendulum machining of components with weights of up to 20 tons, the machine replaced two older machining centers.
While the new machine does save space, two factors are even more important to Buescher: the newly gained flexibility and productivity. “We wanted to implement single-line production, which means that, once they have been welded, several of our construction vehicles‘ main components, such as shovels, excavator arms or front and rear frames, will be conveyed into one central machining center.
“This center must be able to mill different assembly bolt that fits into all of these components, regardless of their sizes and of whether they are intended for a wheel bearing or a mobile excavator. Emco Mecof‘s Ecomill makes it possible for us to master this challenge,” said Buescher.
However, coming up with the current solution has not been easy. Repeated adjustments of the standard machine concept had been required. One of the many challenges involved the full digital integration into production management. What is more, there was only one clearly defined area available for the setup of the machining center, which implied the exact calculation and implementation of the installation site‘s statistics.
Reduced milling time
Compared to the modifications referred to above, only a few changes had to be made to the highlight of the Ecomill, a flexible and infinitely variable universal milling head with A- and B-axes able to perform highly precise horizontal and vertical tasks and, according to Uwe Urban, Emco sales manager for large-scale machinery, the machine‘s centerpiece. “The mechanical design of our compact milling head makes it possible to use relatively short tools, which in turn results in ideal power transmission and high stability,” said Urban.
What is more, the universal milling head comes with pneumatic oil lubrication, a water cooling system, and automatic positioning to the nearest thousandth of a degree. “These innovations allow us to achieve increased precision and productivity about the workpieces,” explains Urban.
This is confirmed by Matthias Henning, production manager of Komatsu Germany, who proves the productivity gain based on H8 fits with a diameter of more than 100 mm which have to be milled into different types of shovels regularly. “It took the old machine a total of 45 minutes to complete the milling process. The Ecomill, however, can do that in only 17 minutes,” he said.
Apart from that, the traveling column machine reduces downtime. While a component is being machined on one side of the machine, the machine operator prepares the next component on the other side.
All the operator needs to do then is select the matching program on the CNC and press the start button. After that, he will keep an eye on the machining process while at the same time setting up a new component. Today, it takes only one employee to carry out all of these work steps.
“In the past, we would need three skilled workers in two machines to complete these tasks,” said Henning. Today, he said he is glad that he has two more employees at his disposal who can work in other departments of the company to reliably and flexibly respond to Komatsu Germany‘s increasing number of customer inquiries.
Contact Details
Related Glossary Terms
- centers
centers
Cone-shaped pins that support a workpiece by one or two ends during machining. The centers fit into holes drilled in the workpiece ends. Centers that turn with the workpiece are called “live” centers; those that do not are called “dead” centers.
- computer numerical control ( CNC)
computer numerical control ( CNC)
Microprocessor-based controller dedicated to a machine tool that permits the creation or modification of parts. Programmed numerical control activates the machine’s servos and spindle drives and controls the various machining operations. See DNC, direct numerical control; NC, numerical control.
- gang cutting ( milling)
gang cutting ( milling)
Machining with several cutters mounted on a single arbor, generally for simultaneous cutting.
- machining center
machining center
CNC machine tool capable of drilling, reaming, tapping, milling and boring. Normally comes with an automatic toolchanger. See automatic toolchanger.
- milling
milling
Machining operation in which metal or other material is removed by applying power to a rotating cutter. In vertical milling, the cutting tool is mounted vertically on the spindle. In horizontal milling, the cutting tool is mounted horizontally, either directly on the spindle or on an arbor. Horizontal milling is further broken down into conventional milling, where the cutter rotates opposite the direction of feed, or “up” into the workpiece; and climb milling, where the cutter rotates in the direction of feed, or “down” into the workpiece. Milling operations include plane or surface milling, endmilling, facemilling, angle milling, form milling and profiling.
- milling machine ( mill)
milling machine ( mill)
Runs endmills and arbor-mounted milling cutters. Features include a head with a spindle that drives the cutters; a column, knee and table that provide motion in the three Cartesian axes; and a base that supports the components and houses the cutting-fluid pump and reservoir. The work is mounted on the table and fed into the rotating cutter or endmill to accomplish the milling steps; vertical milling machines also feed endmills into the work by means of a spindle-mounted quill. Models range from small manual machines to big bed-type and duplex mills. All take one of three basic forms: vertical, horizontal or convertible horizontal/vertical. Vertical machines may be knee-type (the table is mounted on a knee that can be elevated) or bed-type (the table is securely supported and only moves horizontally). In general, horizontal machines are bigger and more powerful, while vertical machines are lighter but more versatile and easier to set up and operate.
- milling machine ( mill)2
milling machine ( mill)
Runs endmills and arbor-mounted milling cutters. Features include a head with a spindle that drives the cutters; a column, knee and table that provide motion in the three Cartesian axes; and a base that supports the components and houses the cutting-fluid pump and reservoir. The work is mounted on the table and fed into the rotating cutter or endmill to accomplish the milling steps; vertical milling machines also feed endmills into the work by means of a spindle-mounted quill. Models range from small manual machines to big bed-type and duplex mills. All take one of three basic forms: vertical, horizontal or convertible horizontal/vertical. Vertical machines may be knee-type (the table is mounted on a knee that can be elevated) or bed-type (the table is securely supported and only moves horizontally). In general, horizontal machines are bigger and more powerful, while vertical machines are lighter but more versatile and easier to set up and operate.