Contact Details
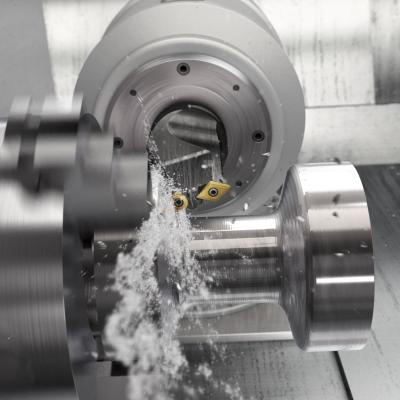
Sandvik Coromant, a cutting tool and tooling system specialist, has introduced a new method for turning complicated shapes and pockets with a single tool. Y-axis turning offers benefits such as reduced cycle time, improved component surface quality and more stable machining.
Turning has developed immensely in recent years with new innovations, such as all-directional PrimeTurning™, non-linear turning and interpolation turning. “One could say that these advances, together with progressive capabilities in modern machines and CAM software, have paved the way for the new Y-axis turning method,” says Staffan Lundström, Product Manager, Turning, at Sandvik Coromant. “And with the tools and method now in place, we look forward to exploring the possibilities this method can present to our customers.”
So how does Y-axis turning work? As the name implies, the new method makes use of the Y-axis, and all three axes are used simultaneously when machining. The tool rotates around its own center, the insert is placed for machining in the Y-Z plane and the milling spindle axis interpolates during turning. This allows intricate shapes to be machined with a single tool.
Y-axis turning offers numerous benefits. The ability to machine several features with a single tool reduces cycle time, and no tool changes are required, which minimizes the risk of “blend points,” or irregularities between adjacent machined surfaces. The main cutting forces are directed into the machine spindle, thus improving stability and reducing the risk of vibration. A constant entering angle drastically improves chip control and makes it easier to avoid chip jamming.
Two new tools have been developed to support Y-axis turning. The new CoroTurn® Prime variant is suitable for shafts, flanges and components with undercuts. The CoroPlex® YT twin-tool, featuring CoroTurn TR profiling inserts and CoroTurn 107 round inserts with rail interface, can favorably be used for components with pockets and cavities.
To summarize, Y-axis turning is a method for simultaneous three-axis turning with interpolation of the milling spindle axis. The new tools can also be used in “static mode” with a locked spindle for flexible two-axis turning with fast insert indexing. The method is suitable for all materials and requires a multitask machine with options to allow interpolation of the milling spindle axis during turning."
Related Glossary Terms
- computer-aided manufacturing ( CAM)
computer-aided manufacturing ( CAM)
Use of computers to control machining and manufacturing processes.
- gang cutting ( milling)
gang cutting ( milling)
Machining with several cutters mounted on a single arbor, generally for simultaneous cutting.
- interpolation
interpolation
Process of generating a sufficient number of positioning commands for the servomotors driving the machine tool so the path of the tool closely approximates the ideal path. See CNC, computer numerical control; NC, numerical control.
- milling
milling
Machining operation in which metal or other material is removed by applying power to a rotating cutter. In vertical milling, the cutting tool is mounted vertically on the spindle. In horizontal milling, the cutting tool is mounted horizontally, either directly on the spindle or on an arbor. Horizontal milling is further broken down into conventional milling, where the cutter rotates opposite the direction of feed, or “up” into the workpiece; and climb milling, where the cutter rotates in the direction of feed, or “down” into the workpiece. Milling operations include plane or surface milling, endmilling, facemilling, angle milling, form milling and profiling.
- profiling
profiling
Machining vertical edges of workpieces having irregular contours; normally performed with an endmill in a vertical spindle on a milling machine or with a profiler, following a pattern. See mill, milling machine.
- turning
turning
Workpiece is held in a chuck, mounted on a face plate or secured between centers and rotated while a cutting tool, normally a single-point tool, is fed into it along its periphery or across its end or face. Takes the form of straight turning (cutting along the periphery of the workpiece); taper turning (creating a taper); step turning (turning different-size diameters on the same work); chamfering (beveling an edge or shoulder); facing (cutting on an end); turning threads (usually external but can be internal); roughing (high-volume metal removal); and finishing (final light cuts). Performed on lathes, turning centers, chucking machines, automatic screw machines and similar machines.