Contact Details
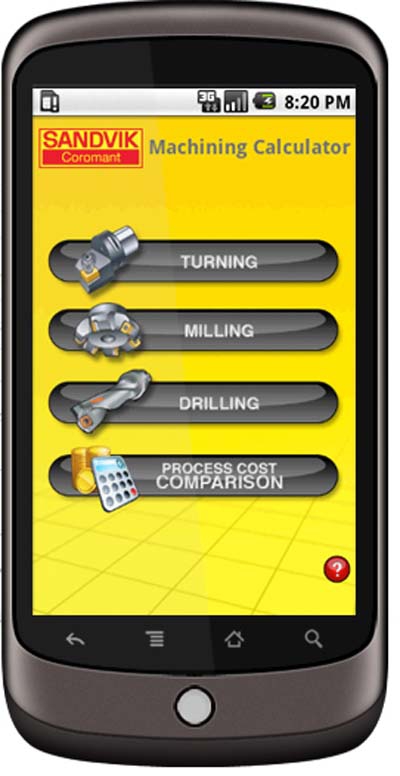
Sandvik Coromant has released a free application designed to provide engineers and machinists with a convenient resource for calculating cutting data. Once downloaded and installed, it helps users optimize performance of their turning, milling and drilling applications by calculating optimal setting based on a job's unique parameters. "We're always looking for exciting new ways to meet the ever-changing needs of our customers," says Lennart Lindgren, global vice president marketing and sales. "We developed this App to provide customers with a convenient resource that can be accessed anywhere they take their phone." The Machining Calculator features a help button that provides additional information on the calculation being executed and the input needed to generate results. Sandvik Coromant's application also contains a process cost comparison that determines how tool optimization can provide cost and time savings. The calculator works with both metric and inch measurements and is available for both iPhone and Android phones.
Related Glossary Terms
- gang cutting ( milling)
gang cutting ( milling)
Machining with several cutters mounted on a single arbor, generally for simultaneous cutting.
- milling
milling
Machining operation in which metal or other material is removed by applying power to a rotating cutter. In vertical milling, the cutting tool is mounted vertically on the spindle. In horizontal milling, the cutting tool is mounted horizontally, either directly on the spindle or on an arbor. Horizontal milling is further broken down into conventional milling, where the cutter rotates opposite the direction of feed, or “up” into the workpiece; and climb milling, where the cutter rotates in the direction of feed, or “down” into the workpiece. Milling operations include plane or surface milling, endmilling, facemilling, angle milling, form milling and profiling.
- turning
turning
Workpiece is held in a chuck, mounted on a face plate or secured between centers and rotated while a cutting tool, normally a single-point tool, is fed into it along its periphery or across its end or face. Takes the form of straight turning (cutting along the periphery of the workpiece); taper turning (creating a taper); step turning (turning different-size diameters on the same work); chamfering (beveling an edge or shoulder); facing (cutting on an end); turning threads (usually external but can be internal); roughing (high-volume metal removal); and finishing (final light cuts). Performed on lathes, turning centers, chucking machines, automatic screw machines and similar machines.