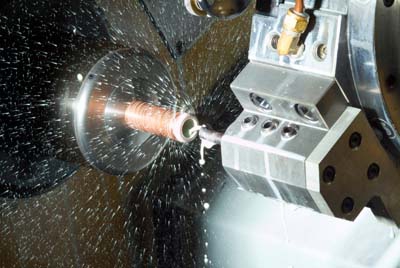
CIMMILL 1350 is fast becoming the fluid of choice in moderate-duty rollforming, threading and cutting operations of ferrous metals. The synthetic product is part of the new CIMMILL line of metalworking fluids formulated to increase productivity by up to 20 percent in tube and pipe operations. The products are manufactured by longtime industry leader CIMCOOL Fluid Technology.
CIMMILL 1350 provides additional lubricity over lighter duty fluids, offers low foam, good chip settling, clean operations, long sump life, corrosion control, and excellent weld-through capabilities. Increased productivity and trouble-free performance make CIMMILL Fluids appropriate for tube and pipe operations.
"We have a history of success in tube and pipe operations, but our new CIMMILL Fluids, including CIMMILL 1350, are designed to significantly improve productivity. CIMMILL Fluids exceed key performance needs of tube and pipe mills while continuing our commitment to always provide operator-safe products," said Bruce Koehler, Cimcool Product Manager.
Contact Details
Related Glossary Terms
- lubricity
lubricity
Measure of the relative efficiency with which a cutting fluid or lubricant reduces friction between surfaces.
- metalworking
metalworking
Any manufacturing process in which metal is processed or machined such that the workpiece is given a new shape. Broadly defined, the term includes processes such as design and layout, heat-treating, material handling and inspection.
- threading
threading
Process of both external (e.g., thread milling) and internal (e.g., tapping, thread milling) cutting, turning and rolling of threads into particular material. Standardized specifications are available to determine the desired results of the threading process. Numerous thread-series designations are written for specific applications. Threading often is performed on a lathe. Specifications such as thread height are critical in determining the strength of the threads. The material used is taken into consideration in determining the expected results of any particular application for that threaded piece. In external threading, a calculated depth is required as well as a particular angle to the cut. To perform internal threading, the exact diameter to bore the hole is critical before threading. The threads are distinguished from one another by the amount of tolerance and/or allowance that is specified. See turning.