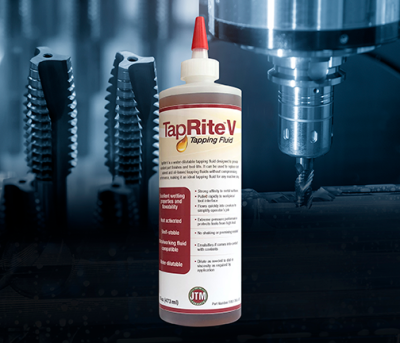
A new high performance, easy to use tapping / threading fluid has been announced by its manufacturer, JTM Products, Inc. TapRite™ V Tapping Fluid (https://koolrite.com/pdfs/tapritev.pdf) is water-dilutable, and designed to replace both solvent and oil-based fluids without compromising performance, providing excellent part finishes as well as extended tool-life. Its performance makes it an ideal “universal” tapping fluid, appropriate for any machine shop.
TapRite V’s advanced formulation provides many benefits to metalworkers. It has excellent wetting properties with a strong affinity to metal surfaces, allowing the fluid to migrate to the workpiece / tool interface faster than similar products. Its exceptional flowability improves handling as well as simplifying the operator’s task by flowing into hard-to-reach crevices during the cut. TapRite V is heat-activated, providing extreme pressure performance to protect tools and workpieces where the cut generates high heat.
Additionally, TapRite V is supplied ready to use, is shelf-stable, and requires no pre-mixing prior to use. Performance is consistent while mixing is eliminated. TapRite V is compatible with metalworking coolants. If an application presents the potential that the tapping fluid may come into contact with metalworking coolants, TapRite V will emulsify into the coolant without causing complications. Finally, by being water-dilutable, TapRite V can be easily dialed-in to the specific viscosity and concentration requirements of an application. Being water-diluted has an additional benefit; it is easier to rinse from the machined workpiece than solvent or oil-based fluids.
TapRite V is available in 16 oz. bottles, one-gallon jugs and in five-gallon pails. Its manufacturer, JTM Products, Inc., has been providing industrial lubricants since 1890 and has been an innovator in water-soluble lubricants since the early 1900s when it introduced the world’s first water-soluble petroleum oil cutting fluid for machine tools.
Contact Details
Related Glossary Terms
- coolant
coolant
Fluid that reduces temperature buildup at the tool/workpiece interface during machining. Normally takes the form of a liquid such as soluble or chemical mixtures (semisynthetic, synthetic) but can be pressurized air or other gas. Because of water’s ability to absorb great quantities of heat, it is widely used as a coolant and vehicle for various cutting compounds, with the water-to-compound ratio varying with the machining task. See cutting fluid; semisynthetic cutting fluid; soluble-oil cutting fluid; synthetic cutting fluid.
- cutting fluid
cutting fluid
Liquid used to improve workpiece machinability, enhance tool life, flush out chips and machining debris, and cool the workpiece and tool. Three basic types are: straight oils; soluble oils, which emulsify in water; and synthetic fluids, which are water-based chemical solutions having no oil. See coolant; semisynthetic cutting fluid; soluble-oil cutting fluid; synthetic cutting fluid.
- metalworking
metalworking
Any manufacturing process in which metal is processed or machined such that the workpiece is given a new shape. Broadly defined, the term includes processes such as design and layout, heat-treating, material handling and inspection.
- tapping
tapping
Machining operation in which a tap, with teeth on its periphery, cuts internal threads in a predrilled hole having a smaller diameter than the tap diameter. Threads are formed by a combined rotary and axial-relative motion between tap and workpiece. See tap.
- threading
threading
Process of both external (e.g., thread milling) and internal (e.g., tapping, thread milling) cutting, turning and rolling of threads into particular material. Standardized specifications are available to determine the desired results of the threading process. Numerous thread-series designations are written for specific applications. Threading often is performed on a lathe. Specifications such as thread height are critical in determining the strength of the threads. The material used is taken into consideration in determining the expected results of any particular application for that threaded piece. In external threading, a calculated depth is required as well as a particular angle to the cut. To perform internal threading, the exact diameter to bore the hole is critical before threading. The threads are distinguished from one another by the amount of tolerance and/or allowance that is specified. See turning.