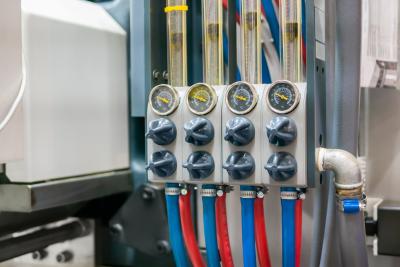
Operation of injection molds and metal presses occurs at high temperatures. As a result, special chillers and cooling systems are often needed to keep machines and workpieces from overheating. But what happens when the tooling is temporarily taken offline? Unfortunately, corrosion can be part of the sad story—a story whose ending Cortec® Corporation bids to change by recommending the addition of VpCI®-649 BD to cooling water.
The Tooling Corrosion Problem
Corrosion inside the cooling water system of an injection mold or metal press is less likely when the equipment is in action and cooling water is flowing. This changes when tooling goes offline either intermittently or for long-term storage. Residual moisture in the system can incite corrosion that remains unnoticed until the equipment is put back into service. Serious complications may result, requiring maintenance to pull the equipment back offline and spend extra time fixing the problem so that work can proceed as normal. The time lost on the job not only represents profit lost but also puts projects at risk for not meeting deadlines.
Adding Corrosion Inhibitors to Cooling Water
One simple solution is to add VpCI®-649 BD to cooling water tanks while the system is operating. This unique concentrated liquid corrosion inhibitor formulation is designed to provide long-term protection for ferrous and non-ferrous metals in water and glycol closed-loop systems. It combines contact corrosion inhibitors with Vapor phase Corrosion Inhibitors. As the water circulates, VpCI®-649 BD forms a corrosion inhibiting film on the metal and continues to protect these surfaces even after the water is drained for offline tooling storage. VpCI®-649 BD also fights scale with the presence of an acrylic polymer. It does not contain nitrite, phosphate, or chromate and is available in a molybdate-free version.
Maintaining Protection
A concentration of 0.5% VpCI®-649 BD may be all that is needed to inhibit corrosion inside the tooling cooling water system. As time passes, this concentration may change as water is lost. Workers should therefore periodically monitor the water (e.g., by the molybdate tracer or refractometer) to make sure the right level of VpCI®-649 BD remains. Additional water or VpCI®-649 BD can be added as needed to maintain the proper concentration of corrosion inhibitor for protection.
A Happy End to Tooling Corrosion
Corrosion is an unwanted intruder inside tooling equipment—even if only in the unseen areas of the cooling system. By simply adding a corrosion inhibitor such as VpCI®-649 BD to the cooling water system during periods of operation, machine shops and injection molders can prepare their high-tech equipment to sit for extended periods of storage without unwanted corrosion surprises when the equipment is brought back online. Contact Cortec® for specific instructions on how to make sure the story of your tooling application has a happy ending!