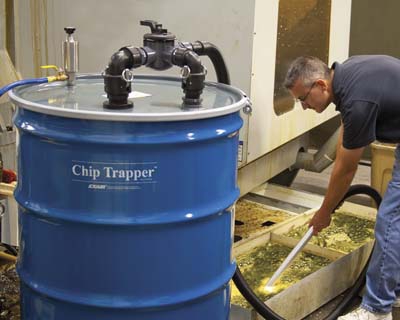
Exair Corp.'s new 110 gallon Chip Trapper offers a fast, easy way to clean large coolant sumps. Chip Trapper removes the solids such as chips, swarf and shavings out of used coolants and other liquids. Coolant that used to last only six weeks can now last six months or more. It is ideal for use on machines with sumps, parts washers, tanks and storage containers. Metal chips in a machine sump can block the intake of the coolant pump, which reduces the coolant flow and causes heat-related damage to the expensive parts and tooling. Regular cleaning of the sump with a Chip Trapper eliminates this problem, the lost production, and downtime. The compressed air powered Chip Trapper vacuums the dirty coolant or liquid into the included 110 gallon drum, trapping all the solids in a reusable filter bag. With a turn of the flow valve, clean liquid pumps back out. There are no motors or impellers to clog or wear out. Safe operation is assured with built-in pressure/vacuum relief and an automatic safety shutoff to prevent spills or overfilling. The Model 6198-110 Chip Trapper includes the stainless steel two-way pump, directional flow valve, 110 gallon drum, lever lock drum lid, shutoff valve, 10' vacuum hose, 20' compressed air hose, chip wand, (2) filter bags and a drum dolly. Price is $1,947. A 55 gallon model and optional Spill Recovery Kit is available.
Contact Details
Related Glossary Terms
- coolant
coolant
Fluid that reduces temperature buildup at the tool/workpiece interface during machining. Normally takes the form of a liquid such as soluble or chemical mixtures (semisynthetic, synthetic) but can be pressurized air or other gas. Because of water’s ability to absorb great quantities of heat, it is widely used as a coolant and vehicle for various cutting compounds, with the water-to-compound ratio varying with the machining task. See cutting fluid; semisynthetic cutting fluid; soluble-oil cutting fluid; synthetic cutting fluid.
- recovery
recovery
Reduction or removal of workhardening effects, without motion of large-angle grain boundaries.
- relief
relief
Space provided behind the cutting edges to prevent rubbing. Sometimes called primary relief. Secondary relief provides additional space behind primary relief. Relief on end teeth is axial relief; relief on side teeth is peripheral relief.
- swarf
swarf
Metal fines and grinding wheel particles generated during grinding.