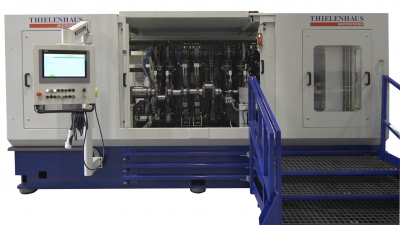
Automobile manufacturers are familiar with the problems associated with the microfinishing of crankshafts. After evaluating statistics from its fleet network, a well-known truck manufacturer has ascertained that a high percentage of reported crankshaft damage is due to particularly large loads on the bearings radii. Working closely with the German high-precision machine tool manufacturer Thielenhaus Microfinish, the truck manufacturer therefore decided to perform finishing work on the bearings as well as on the transition radii. To achieve the same surface quality on the crankshaft journals and radii, Thielenhaus developed a special tape contact shoe. The new RadiusFlex shoe technology presses a finishing tape with a special profile on both sides into the radius, allowing radii to be machined up to 90°. This represents a significant break-through from the previous 60°. The truck manufacturer’s goal was thus successfully achieved.
Innovative machine solutions and tape contact shoe systems open up new possibilities for engine manufacturers and their suppliers, enabling the microfinishing of crankshafts of various designs simpler, faster and more cost-effective.
The shoe systems can all be integrated in Thielenhaus’s CrankStar machine platform, which features horizontal and vertical versions for machining passenger car or truck crankshafts and can be adjusted to the specific needs of each manufacturer. Based on his requirements regarding part handling, cycle times, quality tolerances, part variations and machining tasks, Thielenhaus can develop a machine concept that is precisely tailored to the needs of the customer.
In order to achieve the same roundness improvements on main- and pin bearings, the CrankStar employs pneumatic technology to counterbalance pin bearing forces of +/- 5 Newton. This ensures that the machining forces on the rotating crank pin are kept constant and that the mass forces that occur between the shoe and bearing are compensated. The roundness is thus improved to exactly the same extent on all bearings, whether pin or main bearings.
In the standard version, the CrankStar is capable of machining crankshafts for engines with three to six cylinders, in some cases even without major retooling. In addition to centre and pin bearings and thrust faces, the CrankStar can finish oil seal diameters and deburr bores in the flange. Thrust face machining occurs via a special unit while the workpiece is oscillated. Even with vertical machine concepts, the CrankStar comes with up to 33 percent longer intervals between tool changes than the industry standard, featuring a tape capacity of 300+ metres. The vertical solution allows a quick belt change from the front of the machine, without requiring the withdrawal of an entire tool carrier package.
The leading machine tool manufacturer for microfinishing is developing prototypes and filing patent applications for a variety of other innovative tape contact shoe systems. In addition to the conventional hard or soft shoes, Thielenhaus is developing a shoe that uses a kind of belt system to adapt to the component’s size. With the DiaFlex technology, crankshafts with the same bearing widths but different diameters can be machined without swapping the shoes. In practice, it often happens that, due to higher torques in three- or four-cylinder motors, a few millimetres more of bearing diameter are needed with the same motor concept and gauge. The DiaFlex shoe adapts to the respective diameter and can compensate for differences of up to 15 mm without changing shoes.
Contact Details
Related Glossary Terms
- filing
filing
Operation in which a tool with numerous small teeth is applied manually to round off sharp corners and shoulders and remove burrs and nicks. Although often a manual operation, filing on a power filer or contour band machine with a special filing attachment can be an intermediate step in machining low-volume or one-of-a-kind parts.