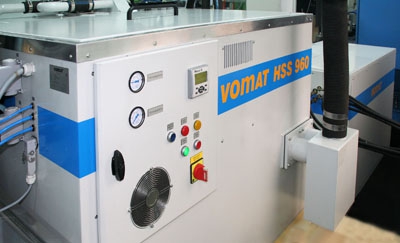
Demanding grinding applications require a powerful filtration system, that positively supports and affects the production process. The filtration specialist Vomat provides the metalworking industry with individually tailored filtration concepts, as well as custom solutions for special applications. One example is a filtration system, which can handle Carbide and HSS waste running on the same machine, which is distributed in the U.S. by Oelheld U.S. Inc.
Filtering of cooling lubricants is an important part in grinding carbide and machining high-speed steels (HSS). Stephan Hecht of Vomat's U.S. exclusive distributor states: "Very often tool manufacturers produce tools, such as a drill made from carbide and HSS on one single machine. The generated waste, especially the HSS swarf clogs up filter cartridges and overtaxes a lot of filtration systems out on the market. Therefore, an efficient pre-filtration is essential in order to achieve continuous micro-filtration."
To solve this problem Vomat developed a special pre-filter. Due to Vomat's modular machine design, it can easily be retrofitted to any Vomat filtration system. After removal of coarse HSS material, the fine filtration of the lubricant starts in the second stage, whereby HSS swarf of 3-5µm in size is removed.
Stephan Hecht: "With this approach the processor of mixed media on one machine is on the safe side. He will always have clean oil to at least NAS 7 available."
Vomat's design uses full stream filtration which always guarantees 100 percent separation of clean and dirty oil. Vomat's filtration systems clean and backwash their filter cartridges only on demand. Back-flushing is automatically initiated in response to the degree of contamination of each individual filter cartridge. The lesser contaminated filter cartridges will remain in service and ensure a continuous supply of clean oil.
The on demand back-flush technology pioneered by Vomat on their mixed media filtration systems, provides also for great energy savings. The the use of newly designed settling filters does not require the use of any other filtration agents and prevents the Carbide sludge and HSS swarfs to be contaminated. The residual moisture content of the chips is below five percent. Besides the manual bag disposal Vomat offers the "Sedimentator" tank with fully automatic sludge disposal into drums, which are ready for pick-up by your preferred recycling company.
Contact Details
Related Glossary Terms
- grinding
grinding
Machining operation in which material is removed from the workpiece by a powered abrasive wheel, stone, belt, paste, sheet, compound, slurry, etc. Takes various forms: surface grinding (creates flat and/or squared surfaces); cylindrical grinding (for external cylindrical and tapered shapes, fillets, undercuts, etc.); centerless grinding; chamfering; thread and form grinding; tool and cutter grinding; offhand grinding; lapping and polishing (grinding with extremely fine grits to create ultrasmooth surfaces); honing; and disc grinding.
- high-speed steels ( HSS)
high-speed steels ( HSS)
Available in two major types: tungsten high-speed steels (designated by letter T having tungsten as the principal alloying element) and molybdenum high-speed steels (designated by letter M having molybdenum as the principal alloying element). The type T high-speed steels containing cobalt have higher wear resistance and greater red (hot) hardness, withstanding cutting temperature up to 1,100º F (590º C). The type T steels are used to fabricate metalcutting tools (milling cutters, drills, reamers and taps), woodworking tools, various types of punches and dies, ball and roller bearings. The type M steels are used for cutting tools and various types of dies.
- high-speed steels ( HSS)2
high-speed steels ( HSS)
Available in two major types: tungsten high-speed steels (designated by letter T having tungsten as the principal alloying element) and molybdenum high-speed steels (designated by letter M having molybdenum as the principal alloying element). The type T high-speed steels containing cobalt have higher wear resistance and greater red (hot) hardness, withstanding cutting temperature up to 1,100º F (590º C). The type T steels are used to fabricate metalcutting tools (milling cutters, drills, reamers and taps), woodworking tools, various types of punches and dies, ball and roller bearings. The type M steels are used for cutting tools and various types of dies.
- metalworking
metalworking
Any manufacturing process in which metal is processed or machined such that the workpiece is given a new shape. Broadly defined, the term includes processes such as design and layout, heat-treating, material handling and inspection.
- swarf
swarf
Metal fines and grinding wheel particles generated during grinding.