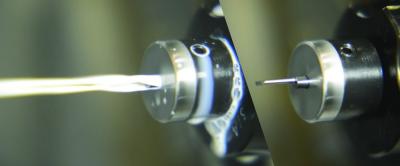
Scientific Cutting Tools offers Coolant Ring Technology holders. CRT holders are made from high-quality heat-treated steel and come with a black-oxide coating. They are engineered to allow for better coolant penetration deep into the bore, reducing temperature at the cutting edge, according to the company. The overhang of the tools used with the holders is infinitely adjustable rather than fixed, allowing for maximum performance without chatter or other performance-related issues. Use the CRT holder in conjunction with the company's qualified boring bars and/or qualified threading tools for quick-change machining at optimal performance levels.
To use the CRT Holders: If you wish to remove the stop, first turn locking screw, with a 3/32 hex key, 1/2 turn counter clockwise. Do not turn locking screw more than one turn or remove locking screw. You can use the same 3/32 hex key for both the adjustable stop and the tool lock down screw.
To insert adjustable stop into the holder: Turn locking screw clockwise until it bottoms out, do not over tighten. Turn locking screw counterclockwise one turn. Line up the locking pin with the keyway in the holder and slide the stop into the holder. Turn the locking screw clockwise until the locking pin bottoms against the keyway.
To set the stop location: Insert a tool into the holder at the desired length of overhang and tighten the tool lock down screw. Slide the stop in the holder until it comes into contact with the back of the tool and tighten the locking screw. Now all other tools will repeat to the same overhang.
If the locking pin is removed from the stop, insert the locking pin into the stop with the countersink facing the locking screw and the long side to the outside of the stop. When the screw is tightened the pin should rise up out of the hole. Snug the locking screw and back off one turn. Now the stop can be inserted into the holder.
Contact Details
Related Glossary Terms
- boring
boring
Enlarging a hole that already has been drilled or cored. Generally, it is an operation of truing the previously drilled hole with a single-point, lathe-type tool. Boring is essentially internal turning, in that usually a single-point cutting tool forms the internal shape. Some tools are available with two cutting edges to balance cutting forces.
- chatter
chatter
Condition of vibration involving the machine, workpiece and cutting tool. Once this condition arises, it is often self-sustaining until the problem is corrected. Chatter can be identified when lines or grooves appear at regular intervals in the workpiece. These lines or grooves are caused by the teeth of the cutter as they vibrate in and out of the workpiece and their spacing depends on the frequency of vibration.
- coolant
coolant
Fluid that reduces temperature buildup at the tool/workpiece interface during machining. Normally takes the form of a liquid such as soluble or chemical mixtures (semisynthetic, synthetic) but can be pressurized air or other gas. Because of water’s ability to absorb great quantities of heat, it is widely used as a coolant and vehicle for various cutting compounds, with the water-to-compound ratio varying with the machining task. See cutting fluid; semisynthetic cutting fluid; soluble-oil cutting fluid; synthetic cutting fluid.
- countersink
countersink
Tool that cuts a sloped depression at the top of a hole to permit a screw head or other object to rest flush with the surface of the workpiece.
- threading
threading
Process of both external (e.g., thread milling) and internal (e.g., tapping, thread milling) cutting, turning and rolling of threads into particular material. Standardized specifications are available to determine the desired results of the threading process. Numerous thread-series designations are written for specific applications. Threading often is performed on a lathe. Specifications such as thread height are critical in determining the strength of the threads. The material used is taken into consideration in determining the expected results of any particular application for that threaded piece. In external threading, a calculated depth is required as well as a particular angle to the cut. To perform internal threading, the exact diameter to bore the hole is critical before threading. The threads are distinguished from one another by the amount of tolerance and/or allowance that is specified. See turning.