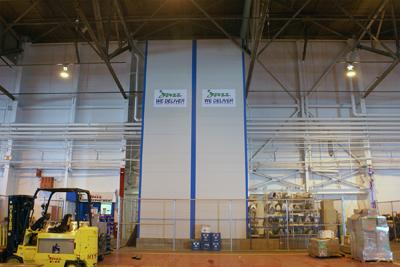
Jazz Aviation is a regional carrier travelling to and from approximately 80 destinations all across Canada and the United States. Working under a commercial agreement with Air Canada, Jazz operates more flights and travels to more Canadian destinations than any other carrier. With flights to big cities, or small town communities, Jazz has a large presence in North America and is one of the largest regional airlines in the world.
The Jazz operational base in Toronto, Ontario is responsible for maintenance and repair operations for 125 airplanes, 24 hours a day, 7 days a week. The largest of six line bases, the maintenance stockroom supplies maintenance and repair parts to technicians on site as well as the other five line bases. This 6,900 square foot facility was limited on space and needed a solution that wouldn't force them to relocate.
"Space is a premium being next to an airport," said Mike Hauser, Stores System Manager. The stockroom already had 200 bays of shelving and with no floor space available, adding more wasn't an option. Overflow bulk inventory was spilling into the hanger reserved for airplane maintenance, and at risk of being misplaced or damaged. "t was a constant battle, we had no more room. We needed a full supply chain solution, not just a temporary fix," said Hauser.
Roughly 1,196 square feet of shelving was consolidated into two Shuttle Vertical Lift Modules (VLMs) from Kardex Remstar occupying only 184 square feet, a 71 percent savings in floor space. Inventory in the two VLMs is managed with Power Pick Global inventory management software that is integrated with existing TRAX software. Further, alongside a four position batch station, additional pick to light technology and label printers add inventory control and increased accuracy levels.
Jazz was able to use the recovered 636 square feet of floor space for storage of bulk inventory. "Part of the goal of this project was to get all of the bulk inventory being stored in the hanger, into the warehouse," said Hauser. "Now all inventory is securely stored in the stockroom providing increased inventory control."
With 20,000 SKUs in inventory, Jazz has to keep a close eye on every part coming in and out of the stockroom. Every SKU received into inventory has a batch, or lot, number. The batch number must be traceable through the distribution channel. It is crucial to know what part number and batch number was used in each airplane.
Upon receipt, each batch is stored in a separate location in the VLMs. If there are 10 of the same part number, but three different batch numbers, Power Pick Global software will store that part in three different locations in the VLMs based on batch number.
Upon picking, the operator must pick a specific part and a specific batch number. This allows Jazz to trace what batch number is put into each order and used on each plane. To verify the pick based on the batch number, the operator scans the part before it goes into the order tote, this ensures they have picked not only the right part number, but the correct batch number as well. Due to the batch picking process and batch validation, accuracy has increased to nearly 99 percent.
Safety is the top priority at Jazz. The protection of inventory is crucial in keeping airplanes at peak performance. VLMs are enclosed units with one access opening to keep stored inventory safe from the natural elements. Using Power Pick Global inventory management software all transactions are logged and traceable, keeping airplanes and passengers safe.
In the old shelving area, it took four to seven minutes per pick, producing about 15 picks per hour. Now in the VLM area, parts are delivered to the operator for picking, eliminating walk and search time. Further, the pick to light technology directs the operator to the exact pick location specifying the location, the part number and the quantity to be picked. Using the VLMs, pick time has increased to an average of one minute per pick, about 60 picks per hour, a productivity increase of 77 percent.
Previously, all SKUs were stored on shelving and pickers would walk up and down aisles, using a pick cart for heavier items. There was one designated ladder stored at the end of each shelving aisle, which was needed to reach the top two rows of shelving.
"Our employees often had to sort through 50 parts to find the correct batch number," said Mike Hauser. "It was a time consuming and labor intensive process."
Once they had gathered all of the SKUs required for an order, employees would bring the parts to a central computer to enter each part picked. Just over half of the 20,000 SKUs in inventory were consolidated into the 2 VLMs. 92 percent of orders come in from technicians and the other 8 percent come from other bases requesting transfers.
The maintenance department enters orders into TRAX, base inventory transfers are created by Supply Chain. The maintenance department creates an order (pick list) in TRAX which auto populates in the Power Pick Global order processing cue. When the operator is ready to fulfill an order, they scan the barcode on the TRAX pick list to populate the order in Power Pick Global.
The batch station located next to the VLMs has four locations, allowing the operator to fill four orders at a time. The VLMs move to retrieve the first SKU required and deliver it to the operator. Using pick to light technology, the TIC (transaction information center) located on the front of each VLM directs the operator to the exact location and displays the quantity to be picked. The operator picks the quantity and scans each SKU's barcode to verify the batch number before distributing the SKUs among the four orders on the batch station. While the operator is distributing the first SKU among the orders, the second VLM is positioning for the next pick, eliminating operator wait time.
After the SKUs are distributed among the orders, the next pick is ready and waiting for the operator. The operator continues to pick from the VLMs until all required SKUs for each order have been retrieved. If the order requires the operator to "break pack," the operator can print a part label during picking and re-label the SKUs picked. Breaking a pack consists of opening a pack of 10 SKUs to pick two for an order.
Using the additional label, the operator "bags and tags" the two SKUs required for the order, maintaining the integrity of the pick. If an order requires inventory from both the VLM area and the shelving area, the VLM parts are picked first. Then the shelving parts are matched up with the order at the staging area where orders are held for pickup.
"We plan to add a third Shuttle VLM to maintain growth and further increase our efficiencies," says Hauser.
With the success of the Jazz's maintenance operation in Toronto, other Jazz maintenance locations are looking to automation to increase their efficiencies.
Contact Details
Related Glossary Terms
- titanium carbide ( TiC)
titanium carbide ( TiC)
Extremely hard material added to tungsten carbide to reduce cratering and built-up edge. Also used as a tool coating. See coated tools.