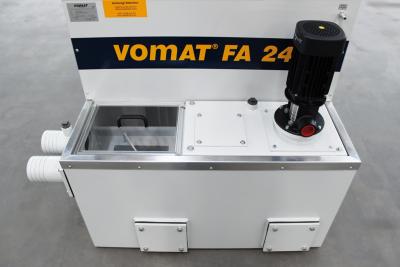
When grinding tools, ultrafine coolant filtration is clearly a worthwhile proposition for the tool manufacturer or regrinder: The cleaner the grinding oil is and the less often it has to be replaced, the more it will save on coolant costs, minimize waste, and reduce tool costs and machine downtimes. Filter technology, which not only cleans the grinding oils and coolants economically, but also keeps them temperature-stabilized state in the system for an extended time period, achieves measurable gains.
Steffen Strobel, technical sales manager of the filter manufacturer VOMAT from Treuen/Germany, said: "Choosing the right filtration and cooling system for grinding oils has a direct effect on the manufacturing costs and the quality of the finished products. It’s important that the coolant is available to the process at a constant temperature and at a high degree of purity over a long period of time. In order to achieve all this, VOMAT filtration systems come in a variety of different versions and are equipped with many special design features."
With VOMAT systems, one can totally avoid the reoccurring operating costs you incur with short-lived disposable filter cartridges or paper band filters. Full-flow filtration with high-performance precoat filters guarantees 100 percent separation of contaminated and clean oil. A special VOMAT design feature allows for the following: Only clean oil is used for the backwash cycle of the filter elements. The cartridges are only back-flushed when required. The on demand backwash cycles are controlled by the degree of contamination in the filter elements and reacts precisely to specific cutting and grinding volumes. This also means that the nominal rated maximum oil quantity, in quality class NAS 7 (3-5 µm), is always available to the process even during backwashing. All this significantly extends the service life of the coolant while also extending the life of the filters. In addition, maintenance costs and machine downtimes are minimized.
Strobel states: "Fluctuating or excessively high temperatures in the cooling medium are detrimental to the process reliability, product quality and service life of the coolant. Modern grinding systems are so sensitive nowadays that they react to minimal temperature changes. Therefore, the filtration system must maintain a constant temperature of the cooling medium. Too high or changing temperatures can cause machine components or the workpiece to expand in nuances, which in turn will result in the finished product being out of tolerance. VOMAT put great importance and effort into designing a cooling system with great control accuracy.”
VOMAT systems permanently cool down cooling lubricants during continuous operation. There are various design options for this: For the VOMAT FA series up to the model FA 240, the cooling unit is available as an integrated slide-in unit. This configuration makes it easy to service the AC-unit without the need for factory service personnel. The condenser is mounted in the hinged hood of the system, and the control accuracy is +/-0.2 K at an ambient temperature of 15° C to 35° C.
In addition, VOMAT offers free standing cooling units with condensers mounted outside the building for FA 120 to FA 960 series systems. The cooling capacity here is 9 to 60 kW with a control accuracy of +/-0.2 K or alternatively +/-1.0 K at ambient temperatures of 15° C to 35° C.
Another option is cold water cooling as a solution with an external cold water circuit. The new Vomat KWS 250 is a modular and expandable chiller with an integrated frequency controlled coolant circulation pump and Eaton compact controls. The cooling capacity is 250 kW for brine operation and it has a control accuracy of +/-1.0 K. No buffer tank is required for the unit and it is also suitable for outdoor installation such as in an industrial park.
Strobel stated: " The VOMAT KWS 250 scores particularly well with its performance and energy efficiency. The chiller consumes up to 62 percent less energy than similar conventional systems. The bottom line is that tool manufacturers and regrinders benefit greatly from machine concepts which are individually adapted to their production-specific needs. In addition, VOMAT systems are low maintenance and make it easy to keep the coolant clean and for a long time. VOMAT can also provide assistance and make adjustments to the systems via online at any time.”
Contact Details
Related Glossary Terms
- bandsaw blade ( band)
bandsaw blade ( band)
Endless band, normally with serrated teeth, that serves as the cutting tool for cutoff or contour band machines.
- coolant
coolant
Fluid that reduces temperature buildup at the tool/workpiece interface during machining. Normally takes the form of a liquid such as soluble or chemical mixtures (semisynthetic, synthetic) but can be pressurized air or other gas. Because of water’s ability to absorb great quantities of heat, it is widely used as a coolant and vehicle for various cutting compounds, with the water-to-compound ratio varying with the machining task. See cutting fluid; semisynthetic cutting fluid; soluble-oil cutting fluid; synthetic cutting fluid.
- grinding
grinding
Machining operation in which material is removed from the workpiece by a powered abrasive wheel, stone, belt, paste, sheet, compound, slurry, etc. Takes various forms: surface grinding (creates flat and/or squared surfaces); cylindrical grinding (for external cylindrical and tapered shapes, fillets, undercuts, etc.); centerless grinding; chamfering; thread and form grinding; tool and cutter grinding; offhand grinding; lapping and polishing (grinding with extremely fine grits to create ultrasmooth surfaces); honing; and disc grinding.
- tolerance
tolerance
Minimum and maximum amount a workpiece dimension is allowed to vary from a set standard and still be acceptable.