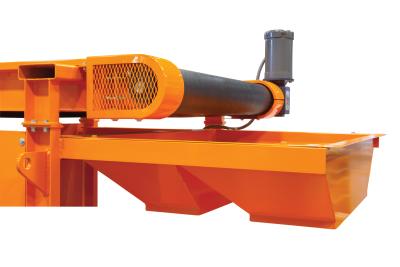
Eriez introduces a rare earth roll conveyor that allows customers to reliably recover and concentrate stainless steel from one of two material streams: “Zurik” conductive fraction from a fines -1” sensor sorting machine or waste fraction (drops) from a fines -1” eddy current separator.
“For wire chopping facilities, this new Rare Earth Roll Conveyor is a game-changer,” said Mike Shattuck, market manager-metals recycling. “It is the most effective solution offered today for removing stray stainless steel prior to any chopping lines.”
Chris Ramsdell, product manager-recycling, explained: “Even a minute amount of stainless steel in the stream can cause expensive damage to blades on wire choppers. Our new rare earth roll conveyor outperforms competitive units with its incredibly high strength rare earth roll. With a magnetic field strength in excess of 20,000 gauss on the roll surface, this is the strongest permanent magnet available anywhere."
Eriez incorporated its decades-long experience manufacturing rare earth rolls into the design of this new conveyor. The conveyor is designed on 5’ centers with a high-strength magnetic head pulley (the rare earth roll). It features a 17-mil Kevlar belt to convey material over the rare earth roll. The belt is very thin to provide for maximum magnetic field strength on the belt surface, but the Kevlar material is also high strength for wear resistance. At the discharge of the rare earth roll (magnetic head pulley), an adjustable splitter assembly provides a split between a weakly magnetic stainless steel fraction and a nonmagnetic material fraction.
Eriez notes that input material must be magnetically treated prior to reaching the conveyor to avoid damage to the belt. Eriez experts work with customers to design a complete system to remove any ferrous materials with drum magnets and/or magnetic head pulleys prior to processing on the conveyor.
Contact Details
Related Glossary Terms
- centers
centers
Cone-shaped pins that support a workpiece by one or two ends during machining. The centers fit into holes drilled in the workpiece ends. Centers that turn with the workpiece are called “live” centers; those that do not are called “dead” centers.
- wear resistance
wear resistance
Ability of the tool to withstand stresses that cause it to wear during cutting; an attribute linked to alloy composition, base material, thermal conditions, type of tooling and operation and other variables.