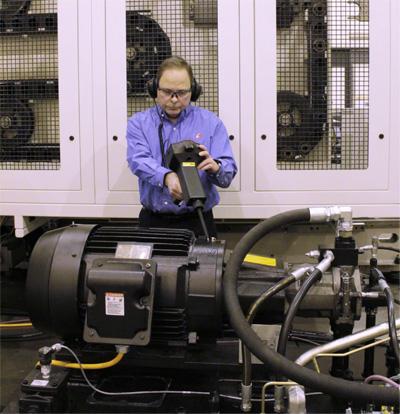
Fives Global Services' new ProCheck machinery evaluation provides a detailed report on the condition and capability of machine tools and other major plant equipment, before purchasing or using systems for critical manufacturing.
"Predictive maintenance inspections with ProCheck help avert unscheduled downtime and reduce scrap by ensuring machine tool capability before running critical parts," said Gary Finney, Vice President and General Manager of Fives Global Services. "A ProCheck inspection takes less than three hours and includes a detailed report, all for $600 per machine."
A ProCheck inspection for machine tools begins with a 3-axis ballbar test that evaluates 11 areas including circularity, squareness, backlash, axis reversal spikes and straightness.
Other tests include:
• Measurement of spindle clamping force and runout.
• Ultrasonic scanning of critical plant/machine systems for bearing vibration/noise, air leaks, pump cavitation, and electrical anomalies.
• Infrared thermographic inspection of bearings, motors, pumps and electrical systems.
• Refractometer testing of coolant condition, concentration and pH level, as well as measurement of tramp oils.
• Ground loop and current leakage testing of electrical systems.
According to Fives Manager of Technology Solutions Mel Gay,the ProCheck package of services isunique in its scope and low cost. "A ballbar check alone can cost $1000 from an outside contractor, but ProCheck includes inspection of multiple machine systems, with a variety of appropriate tools, by a person trained in using those tools," he said. "As a builder of large machining systems, we have a unique background in managing the 'health' of complex equipment, and ProCheck offers that capability to the industry for a nominal cost."
Contact Details
Related Glossary Terms
- backlash
backlash
Reaction in dynamic motion systems where potential energy that was created while the object was in motion is released when the object stops. Release of this potential energy or inertia causes the device to quickly snap backward relative to the last direction of motion. Backlash can cause a system’s final resting position to be different from what was intended and from where the control system intended to stop the device.
- coolant
coolant
Fluid that reduces temperature buildup at the tool/workpiece interface during machining. Normally takes the form of a liquid such as soluble or chemical mixtures (semisynthetic, synthetic) but can be pressurized air or other gas. Because of water’s ability to absorb great quantities of heat, it is widely used as a coolant and vehicle for various cutting compounds, with the water-to-compound ratio varying with the machining task. See cutting fluid; semisynthetic cutting fluid; soluble-oil cutting fluid; synthetic cutting fluid.
- refractometer
refractometer
Optical instrument that measures the refractive index of a liquid, such as a water-diluted metalworking fluid mix. The refractive index can by used to determine the concentration of a fresh metalworking fluid mix.